Selecting a centrifugal pump suitable for handling corrosive liquids presents a few challenges. Not least the selection of materials of construction and how to effectively seal the liquid inside the pump.
The material selection will obviously depend upon the characteristics of the chemical involved and can range from stainless steel (in various grades) to more exotic high nickel alloys. In the past glass or ceramic lined pumps were often a viable solution though this option has largely been replaced by a wide choice of engineered plastics. Such as Polypropylene, PVC, PVDF, PTFE, ETFE, Polyethylene, etc., plastic pumps are available as machined from solid, moulded or lined metallic casings. There are many corrosion resistance charts available online for general guidance. However, for more specific information it is best to speak to the pump manufacturer who will advise on the best engineering and most cost effective solution.
With reference to sealing, it is generally a choice between magnetic drive and mechanical seals, where a rotating element runs against a clamped stationary element. A magnetic drive pump can often be the simpler option as the containment can that separates the driving from the driven magnets simply cannot leak. However, there are applications, such as when pumping liquids with solids content or a high specific gravity, when a magnetic drive pump is unsuitable, then there is no option but to use a mechanically sealed pump.
There are many types of mechanical seals available from a number of manufacturers but for general purpose applications they can be split into single or double seal. Single seals can either be mounted internally, often with stainless steel springs and rubber components exposed to the liquid so suitable for less aggressive liquids, or externally where the materials that see the corrosive liquid are often PTFE, carbon, ceramic or silicon carbide.
For chemicals that contain solids or are a hazard to the environment a double seal can be supplied, this will often require an external flushing system that is often pressurised to above the maximum discharge pressure the pump can achieve, this may sound complicated but once correctly set up this system offers many advantages and may even allow the pump to run dry.
Crest pumps have been manufacturing corrosion resistant centrifugal pumps since 1973 and are hugely experienced in this field. Please do not hesitate to contact us for more advice or a quotation against a specific application.
View the whole mech sealed pumps range
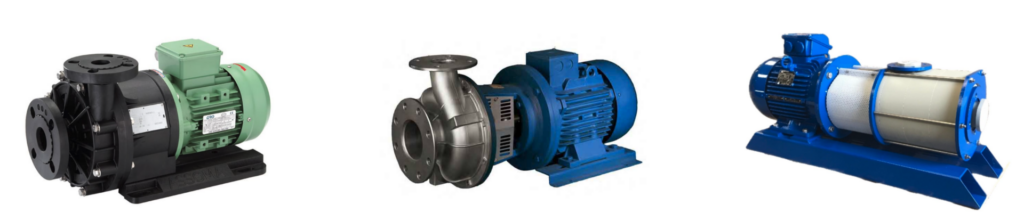