While a pump may be one of the least expensive assets on site, the ultimate price tag of unusable critical spares can be millions of dollars if production is shut down for weeks or months while waiting for a replacement to be delivered. That is why Cortec® Corporation recommends advance budgeting for corrosion protection as a critical part of industrial facility management, especially in the energy sector. Since the urgency of the matter is often not realized until a failure or accident occurs, the tips below are intended to help maintenance, purchasing, or corporate teams start budgeting for that important step of VpCI® preservation before an emergency happens.
Tip 1: Do a Cost-Benefit Analysis
Maintenance and purchasing departments are often evaluated based on how much money they save, not on how many headaches they avoid. It is therefore helpful to do an overall cost-benefit analysis before presenting a preservation budget to superiors. This should take into consideration asset value, cost of restoration, cost of shutdown, safety factors, and lead time for replacement parts. The last three factors are especially critical. Although millions of dollars of assets often sit unprotected in an oil and gas facility yard or warehouse, the true price of losing an asset to rust is the cost of losing the equipment’s function. What happens if there is no replacement for a critical part? What is the estimated loss of production per day? While a typical approach is to say, “Just get a new part,” this is easier said than done. Many refineries are located in distant areas where shipment itself takes a long time. If there is a supply shortage or the asset is a custom part, procurement may be delayed for months or years longer. The effect of these delays must be considered, as well as the potential safety risks if one were to install a rusty part.
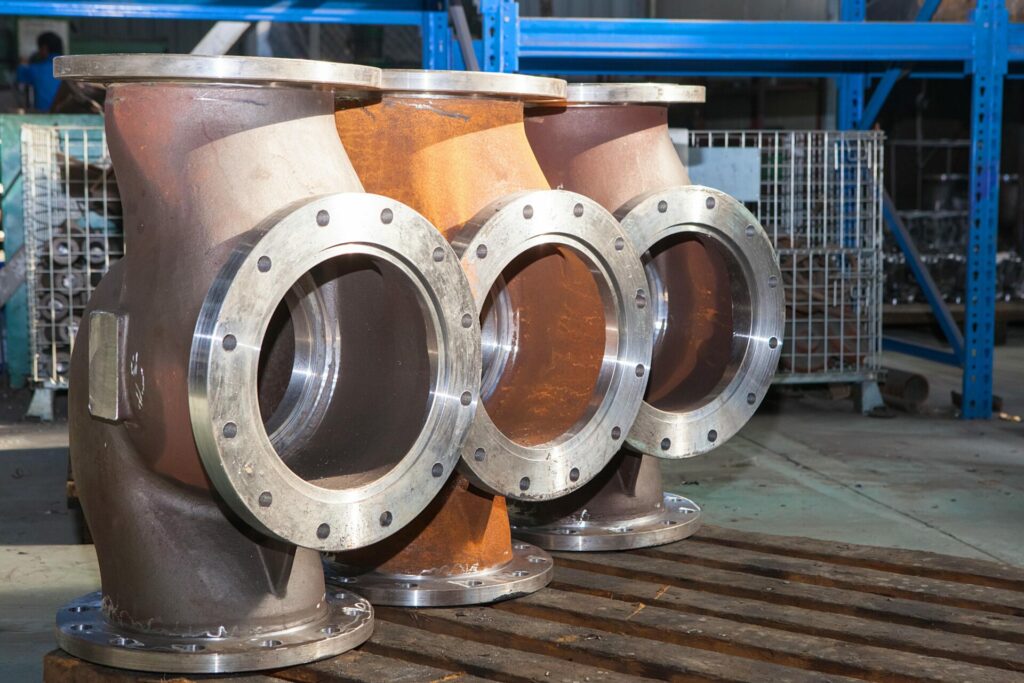
Tip 2: Find a Preservation Advocate
Often, critical preservation does not happen without someone taking ownership of the problem. Understandably, most departments will not want to take responsibility for a preservation budget that has no immediate return and just looks like another request for more money. Maintenance may shift the responsibility to purchasing, and vice versa. Workers may know there is a problem but not be heard. If this is the case, the first step is to appeal to company specifications, which almost always include a preservation requirement and essentially obligate corporate management to provide funding. How much money management is willing to allot may depend on the size of the facility, so maintenance and purchasing departments should leverage this factor in their discussions when appropriate based on the potential impact of failure. Whether maintenance or purchasing should take the bulk of the responsibility depends on whether the assets are warehouse spares (maintenance jurisdiction) or new incoming equipment that needs preservation until installation (purchasing jurisdiction). If management is still ignoring requests, sometimes all that is needed is to call in a preservation consultant to reiterate what employees have been saying all along and advocate for change.
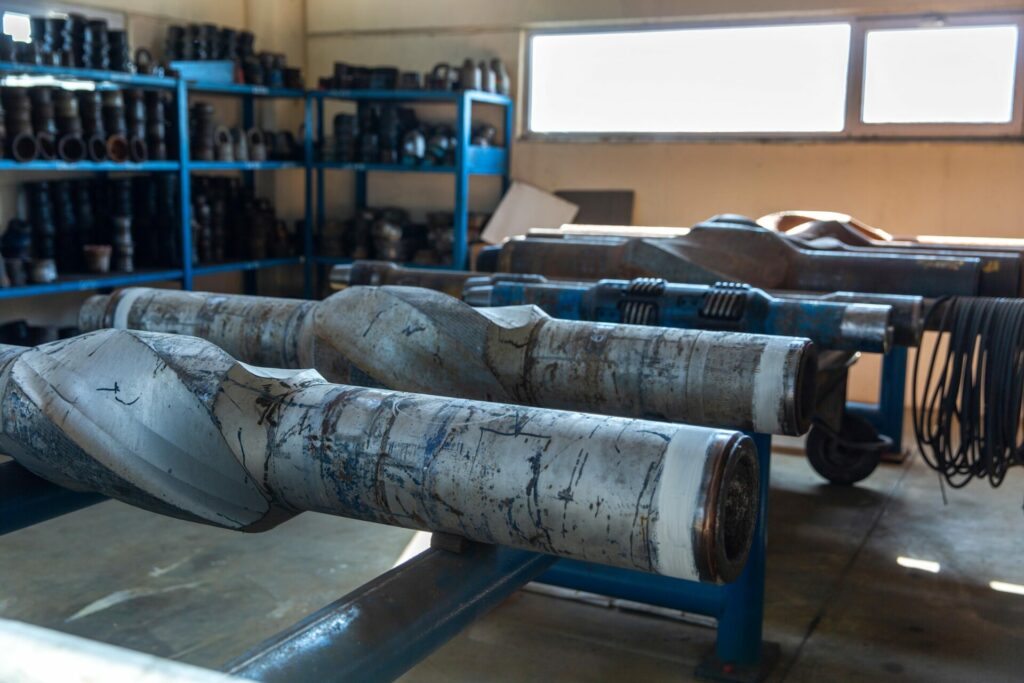
Tip 3: Estimate Preservation Costs
Once management has approved a preservation budget, the appropriate department will want to call in a preservation services company to evaluate preservation needs and estimate total costs, if they have not already. The service provider may evaluate the condition and value of assets onsite, then calculate Cortec® VpCI® material costs, worker costs, and estimated days needed to reach a stable state. The preservation services provider may offer full turnkey preservation services or simply training and materials to the facility’s existing employees. Estimating the full costs of these preservation options will help departments provide a more precise budget to management for further review, discussion, and final decision-making.
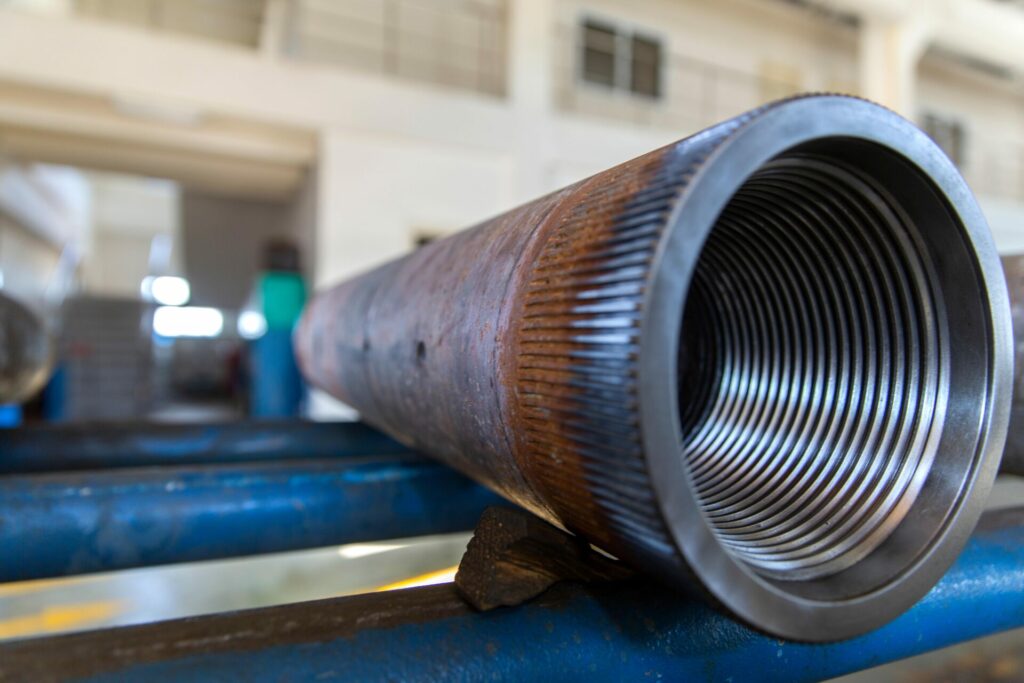
Well Worth the Cost
The initial cost of preservation is negligible compared to the multiple millions of dollars’ worth of assets saved, not to mention the tens or hundreds of millions of dollars that might otherwise be lost from an extended shutdown. Over and above this is the intangible value of protecting worker safety. When taking these factors into account, budgeting for asset preservation is well worth the cost. Contact Cortec® Corporation to learn more about preservation materials and recommended preservation service providers in your region: https://www.cortecvci.com/