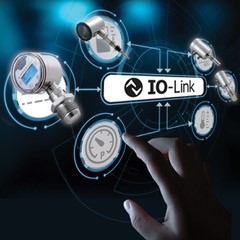
Anderson-Negele is currently equipping its portfolio of hygienic measurement technology with the digital interface IO-Link. With the new turbidity sensor ITM-51, sensors for conductivity, turbidity and level are now available, and soon the measuring ranges pressure, temperature and flow will be available. A special hybrid technology is used here: In addition to the classic analog 4…20 mA interface, the digital IO-Link is supplemented in parallel, so that the advantages of both worlds can be used at any time. A later changeover to digital technology is thus also possible at any time without changing the hardware.
Proven industry standard now also for hygienic and aseptic applications
With IO-Link, you can reliably manage all aspects of process control and bring all measuring points, control devices, and operating elements into one dependable system. After extensive suitability testing, Anderson-Negele is using this technology as the data transfer standard in sanitary application across the food, beverage, and pharmaceutical industries.
The (R)evolution in sensing technology
IO-Link is comparable to a multi-lane data highway instead of a narrow one-way street. It enables continuous, bi-directional digital communication from the highest to the lowest level providing both time and cost savings.
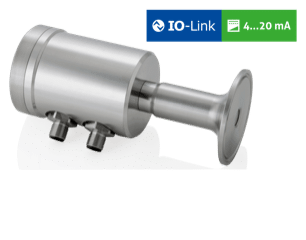
A three-pole standard cable is all that is needed for interference free signal transmission and power supply (no special shielding required). A wide variety of sensors can be connected to the IO-Link Master using a point-to-point connection, which acts as a bridge to the control center via a wide variety of fieldbus systems.
Simply by connecting a new cable, the sensor is easily converted from analog to digital without having to touch the hardware or change any settings.
With IO-Link, data can be transmitted to the control center and back out to the sensor allowing individual sensors to be set, queried and checked at any time. This makes it possible to detect potential faults, signs of wear and increased risk of failure at an early stage. Maintenance work can be planned according to true need, and production downtimes can be minimized.
“Plug-and-Play” has a totally new meaning
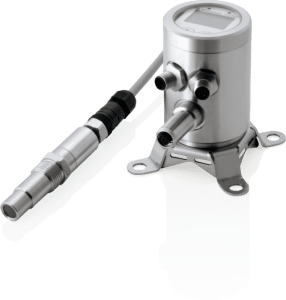
With IO-Link, sensor replacement is easier and safer than ever and can be carried out independently, at any time, with no programming knowledge needed. The complete configuration of each connected sensor can be stored in the IO-Link Master. The new sensor is automatically recognized, configured and parameterized by the IO-Link Master when plugged in. Your new sensor is immediately ready for use.
Equipped for the digital changeover: Modular sensor platform with IO-Link AND 4…20 mA
The hybrid sensors based on Anderson-Negele’s modular platform combine the best of two worlds: from the sensor, data can be transmitted in digital, analog, or parallel in both technologies. This creates an important advantage, especially in times of technological change from today’s analog to the digital generation 4.0: If, for example, a plant is currently still controlled in analog mode, but a conversion to IO-Link is being considered, the customer no longer has to make a decision. Instead of “either … or”, Anderson-Negele uses “and”. Simply by connecting a new cable, the sensor is simply converted to digital without even having to touch the hardware or the settings. Even for sensors of the modular platform already installed in plants, an upgrade to IO-Link can be carried out in just a few steps. This is made possible by exchanging the signal module, which can easily be done on site.
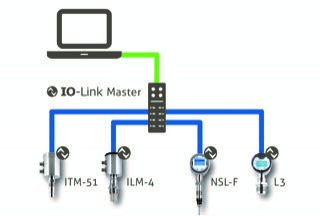
The new dimension of hygienic measurement technology is hybrid and modular
IO-Link, alone, is a big step towards Industry 4.0 in hygienic process technology. With its application-specific configuration, the modular sensor platform offers equipment that is tailored to meet your requirements, cost-optimized, and enables simple replacement of individual components (e.g., displays, electronics). The optional remote version features separate sensors and electronics housing. The electronics are identical for all sensor types and are recognized independently. This “Smart Replace Design” means each sensor can be replaced simply by plugging in the cable and one replacement unit of electronics housing and cable is enough for all sensors.