After all, longer downtimes are not economically viable. And employees with the appropriate expertise are needed. Their maintenance work is made easier when they only have to be familiar with five different pump types in their own company, instead of twenty.
A German company specializes in the disposal and recycling of hazardous waste. The company uses around 50 special vehicles to collect residual materials, such as used oils, gasoline, refrigerant fluids, brake fluids, solvents and several other products from industrial companies, mechanic workshops or car repair shops. The residual materials are then recycled in modern plants using innovative methods. This results in products that can be reused in industry, such as base oils, lubricating oils, flux oils, heating oils and solvents, which are sold in batches of 25,000 liters or more.
Tankers, some with three pumps
The waste is collected from customers all over Europe. A fleet of 22 tankers stands ready to do so. A regular truck fitted with a tank is sufficient for collecting mainly used oil from major customers. For smaller orders, it is logistically advantageous if a vehicle can drive to several customers along a route. However, since different residues are often picked up, different containers are required. As such, in 12 of the vehicles, the tank is divided into three separate compartments, with a respective capacity from 2,000 to 12,500 liters. To enable optimal processing of the waste materials later on, it is crucial that they be loaded with their own kind and without contamination. To make this possible, each tank compartment needs its own pump and feed line for filling. For example, a truck can simultaneously transport brake oils, glycols and water/oil-water mixtures without the substances coming into contact with one another. However, to install three pumps on a vehicle, small pumps would have to be used. The recycling company therefore equipped all the tankers with rotary lobe pumps from the Vogelsang VX 136 series. These are small, yet still deliver the required high operational force – pumping capacities of up to 364 m3/ h and pressures up to 12 bar. The VX136 model has been in use here for 15 years. The gear and progressive cavity pumps previously used had problems pumping brake fluids and ran dry. In order to increase the service life of Vogelsang rotary lobe pumps even further, lobes made of various materials were tested. During testing it was discovered that coated lobes made of FPM are very robust and hold up as desired against materials such as brake oils.
Distillation: Pumps run non-stop
At the company’s premises, approx. 50,000 m2, the collected residues are pumped into tanks. The distillation systems are fed from these large tanks, which range from 100 to 500 m3. There are a total of seven distillation lines that recycle different solvents and oils here. This includes additional ancillary systems, such as the energy center, or exhaust air purification system, as well as an upstream desedimentation system that removes sediments from the input materials for a trouble-free distillation process. Vogelsang rotary lobe pumps are also used here. They are robust against foreign bodies such as metals, stones and sand, since an adapted housing design, the InjectionSystem, delivers these foreign bodies directly into the open cavities of the pump and prevents harmful collisions with the lobe tips. For distillation, it’s crucial that the systems be fed evenly. They operate around the clock, 365 days a year. Accordingly, the pumps for collecting used oil and other substances also run non-stop. Long service lives are therefore essential. Feeding is controlled automatically by a variable frequency drive that controls the number of cubic meters pumped by the system. The volume flow varies between 1 and 150 m3/h. Vogelsang pumps can also load up to a temperature of 80 °C. The HiFlo lobes with curved blades minimize pressure surges and ensure even, pulsation-free pumping. Temperatures within the distillation line rise to 360 °C. Heat-resistant centrifugal pumps are used here as well as for the cooling tower.
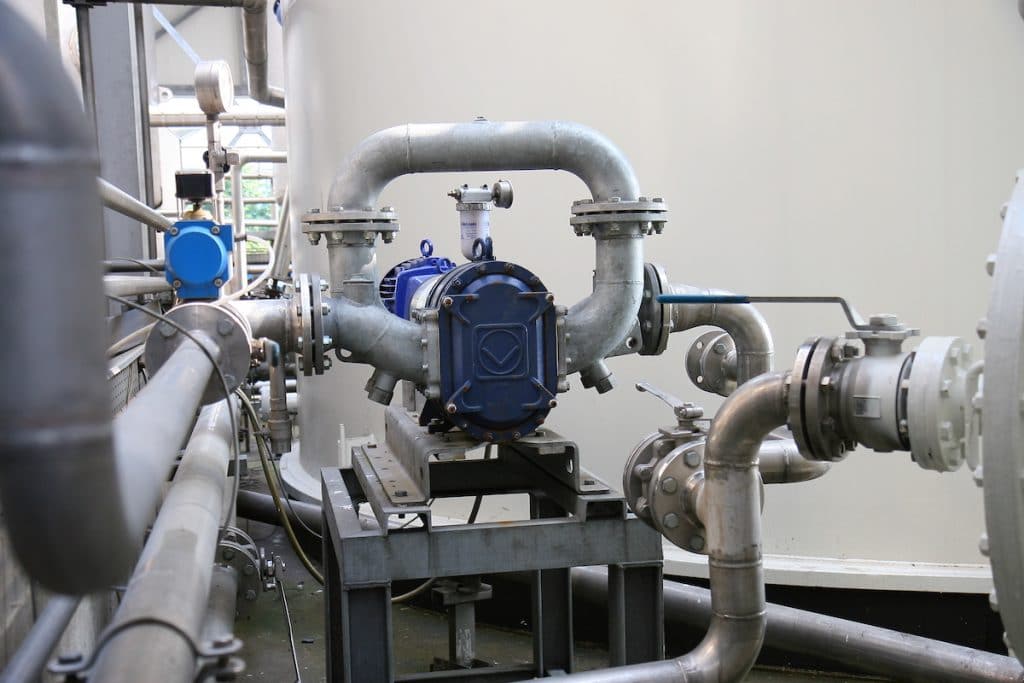
Maintaining over a hundred pumps is a challenge
In total, the company has over a hundred pumps in operation.
Rotary lobe pumps are mainly used on tanks and vehicles. They are compact, powerful and very easy to maintain. In comparison, the centrifugal pumps used are cheaper to operate because they consume less electricity at higher outputs. On the other hand, rotary lobe pumps are more economical when it comes to maintenance. They require fewer spare parts and have a longer service life. Moreover, they can be repaired on-site without being disassembled, which saves time. Due to their QuickService design, only a few steps are needed to replace lobes and seals. The responsible employees learn this quickly and easily. That is why the IQ series is now also available, which requires only half as many spare parts as a conventional design. This considerably reduces the costs for components that need to be replaced and makes handling easier. The pump housing is made from a single complete part. Once the cover has been removed, the inside of the pump can be freely accessed straight away.