This characteristic is very useful in power transmission systems such as hydraulic pistons, however, can lead to catastrophic accidents in piping systems.
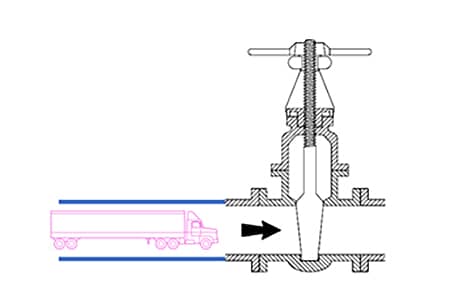
The phenomenon of water hammer is based on this principle, when a volume of a fluid moves through a pipe carries inertia due to its weight, if we close a valve quickly, we are suddenly stopping the movement of this volume, which creates an abrupt increase of pressure, this energy has no way to dissipate or be absorbed due to the non-elasticity property of the fluid, so a wave is created that travels through the pipe until it finds a way to dissipate the energy.
The larger the volume, the greater the pressure spike, similar to what would happen if a truck hits a wall at high speeds, so in large pipes, this phenomenon can cause catastrophic damage.
How to operate valves to reduce or prevent water hammer?
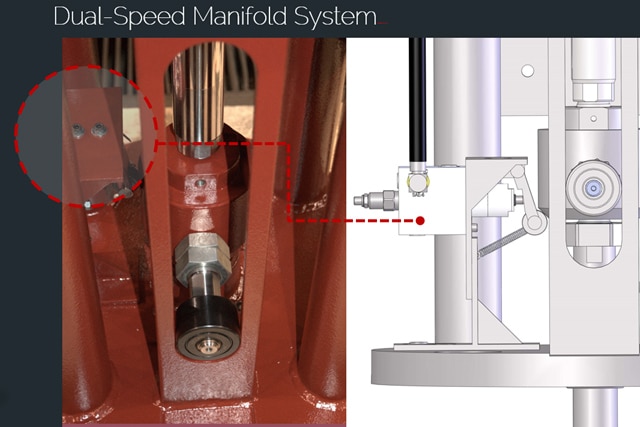
This phenomenon can be reduced prevented by lengthening the time in which changes to the fluid movements are made. In pipes, this is normally done by lengthening the valve’s closing time to create an energy dissipation across it due to pressure loss.
Since valves that will need to close or open quickly are most likely isolation or on/off valves, by design they should not remain partially open for long periods Since this could create damages to the closing membrane, the seats, and other parts due to erosion. This problem can be addressed by using a dual-speed system to operate the valve.
This system will allow the operator to close most of the valve stroke e.g 80% at a fast speed and reduce it in the remaining 20% to ensure the max energy dissipation in the shortest time. The times required to make changes to the fluid are calculated by doing a transit analysis of the piping system.
Another common way to reduce this phenomenon is, based on the previous example of the truck, by reducing the velocity of the fluid. As we know, the speed is dependent on the diameter of the pipe, if the same flow passes through a pipe with a larger diameter, it will pass at a lower velocity.
At Cowan Dynamics we specialize in valve automation, understanding how important is to ensure the right operational times for your valves, we have incorporated variable speeds as standard in our lines of electrohydraulic actuators (E2H, E2HR) and a dual-speed module in our standard double and single acting hydraulic actuators (ML,MS). Variable speed configurations can also be custom made when using any other of our actuation products.
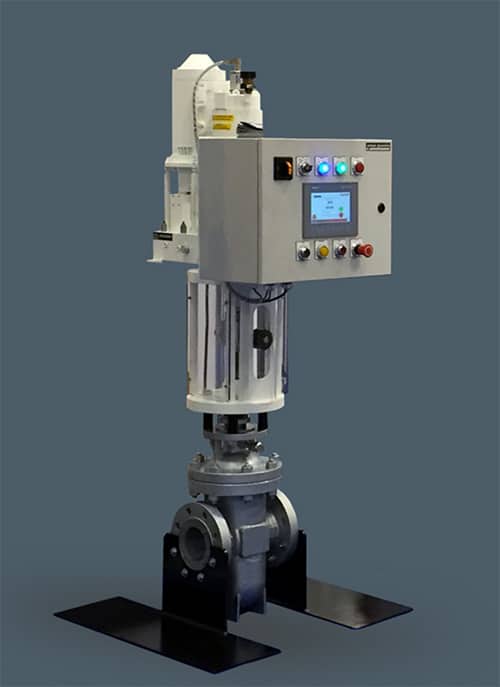
ML Series
Double-Acting Hydraulic Actuator
Compact. Simple. Versatile. Delivering thrust up to 1,500,000 lbs and SIL-3 Capable. Our double-acting hydraulic valve actuators are designed to suit a wide range of applications; from commodity to severe-service extremes.