That being said, the importance of those terms would appear to make words like “fast” and “quick” incompatible with the production of biopharmaceuticals. However, that is not necessarily the case. You see, the most successful biopharmaceutical manufacturers are those that can reliably produce important drugs that are safe for human use while also getting them to market in a timely manner that maximizes the earning potential of patent windows.
This is where pumps become a critical part of the equation. Today’s most common biopharmaceutical-manufacturing systems require the handling, transferring, processing and purification of large-molecule drugs produced in living organism like animal-cell cultures, bacterial cells or yeast. This must be done in a liquid phase with the handling of these materials performed by pump technologies that can reliably provide volumetric consistency and accuracy, pressures and flow rates, and low-pulsation, which are required in the process, and low-shear, low-heat input and material compatibility that protects the biological drug from being harmed.
In general, the manufacturing process is separated in two main stages: The first is upstream processing, in which genetically modified cells suspended in liquid culture media are grown in bioreactors to produce the desired product. The second stage is the separation and purification of the target molecule from the cells and byproducts, which is called downstream processing. Traditionally, permanent stainless-steel pumping and processing systems have been used for these operations, but the time and cost needed to operate, clean, maintain and quality control the system before the next production run could commence became prohibitive. That led to a true innovation for the industry, the creation of single-use pumps that feature a disposable pump head and chamber that can be easily removed and replaced between production runs, eliminating the time and cost needed to revalidate the equipment in a stainless-steel system.
While single-use pumps have been an undoubted boon to biopharmaceutical manufacturers – with positive displacement quaternary (four-piston) diaphragm pumps becoming a go-to technology choice for many manufacturers – there were still improvements that could be made in optimizing their changeover times and simplifying the installation process. A breakthrough in this area came in 2017 with the development of a pump-chamber replacing system that reduces the time needed to replace a disposable single-use pump chamber to mere seconds.
Know Your Unit Operations
First, we should take a step back and give some context to just how significant “complex,” “precise” and “pure” are to the biopharmaceutical-manufacturing process. The foundation of biopharmaceutical manufacturing rests on various types of unit operations. While each unit operation features its own set of operational criteria, they are alike in that they can only produce a viable, contaminant-free drug suitable for human administration if the manufacturer strictly adheres to an unbending set of operational parameters and structures.
Here’s an overview of four of the more common unit operations in biopharmaceutical manufacturing:
- Tangential Flow Filtration (TFF) – Also known as cross-flow filtration, in this process the biopharmaceutical’s feed stream flows tangentially across the filter membrane at positive pressure. As it passes across the membrane, the portion of the feed stream’s molecules that are smaller than the membrane’s pore size pass through the membrane. TFF is different from what is known as normal-flow (NFF), or “dead-end,” filtration, in which the feed flows entirely through the filter membrane with the size of the pores determining which portion of the feed is allowed to pass through and which will remain trapped in the filter membrane. TFF also differs from NFF because the tangential motion of the fluid across the membrane causes any trapped molecules to be “rubbed” off, which eliminates the formation of a gel layer that would lead to blocking of the membrane. This mode of operation means that a TFF process can operate with relatively high product-load without any fouling (blocking) of the filter. Typically, a membrane pore size is selected that retracts the target molecule in the so-called retentate. The portion of small molecules, including water, that will pass the membrane is called permeate. The result is a high concentration of the target molecules in the retentate.
- Chromatography Columns – While TFF is used to concentrate the product based on the molecule size, chromatography is a process that is used to purify target molecules from the other process stream based on adsorption to a resin. This resin is compressed and immobilized in a so-called chromatography column. When the product is pumped through this column, the target molecule can bind (adsorp) under specific conditions at the chromatography resin, while contaminants either do not adsorb or can be washed off. By changing the conditions again (e.g. pH level or conductivity) the target molecules will be released (eluted) from the resin and collected separately from the other process stream to achieve a purified product. Chromatography columns contain expensive media that need careful handling. Protein A resin, for example, can cost many thousands of dollars an ounce, making proper feeding of the resin extremely important. In this application, pumps are used to pack the resin into the chromatography column and then pump the biopharmaceutical material through the column. Both are critical operations that require a high, constant flow rate and pressure.
- Virus Filtration – These systems are used to ensure the safety of the drugs that are produced. They do this through the removal of potential virus particles via constant pumping pressures with variable flow rates. Most typical virus-filtration systems run at a constant pressure due to the nature of the tight pores in the filtering medium, but the flow rates will decrease as the filter’s pores become fouled. When this happens, the flow rate will not decrease in a linear fashion, which will adversely affect the performance of the filter, product yield and overall quality. To combat this phenomenon, pumps that combine a high turndown ratio with minimal pulsation in the pumped fluid are used.
The common thread between these various types of unit operations is their need for and use of a pumping technology that can satisfy their specific operational parameters. Again, these unit operations are processes in which the quaternary diaphragm pump excels, while competitive technologies, such as peristaltic (hose), lobe, centrifugal and piston pumps, may struggle to meet a series of strict product-handling and -transfer requirements.
The Single-Use Solution
Some additional mention must also be given to the advantages that utilizing single-use quaternary diaphragm pumps in biopharmaceutical manufacturing can deliver. The main advantage for these pumps – whether used in traditional stainless-steel or single-use setups – are their unique form of operation: The four quaternary diaphragms are driven one after another by a connector plate, which moves back and forth out of its central position in a stroke that is generated by an eccentric shaft, with the length of the stroke determined by the angle of the eccentricity. The four pumping chambers, which actually operate in the same way the human heart does, keep the product flow constantly moving forward in a volumetrically consistent low-shear and low-pulse manner.
The pump’s chambers also contain no rotating parts that can be subject to friction, meaning that there is minimum heat buildup that can compromise the product. This mode of operation means that the pumps can run dry, are self-priming, and produce minimal shear because of low slip. In addition, they offer low-pulsation, leak-free operation while having great dry/wet suction-lift capabilities.
This turndown capability and range for quaternary diaphragm pumps is also unique in the biopharmaceutical industry. As the products go from development to clinical trials and then to commercialization, proper scaleup is essential. In other words, the same pump in a lab may need to handle flow rates as low as 1/2-ounce per minute while also being able to deliver commercial production flow rates of 50 gallons per minute or more.
The quaternary diaphragm pump is also easily adaptable to single-use production configurations. A single-use pump enables biopharmaceutical manufacturers to essentially eliminate the oftentimes-prohibitive cost of cleaning and validating their pumps and systems. The result is a quicker and more cost-effective production process and one that still delivers preferred levels of product purity and sterility with no chance for cross-batch or cross-product contamination.
The fulcrum of the single-use pump is its product-wetted plastic pump chamber that can be replaced as a complete unit.
The Next Step Forward
So, now we arrive at the next step in the evolution of the single-use quaternary diaphragm pump that is used in unit operations within biopharmaceutical manufacturing. While single-use pump technology conquered the question of how to reduce cleaning and revalidation time and costs after production runs, there was still more ground that could be plowed in the realm of reducing the time needed for pump-head replacement.
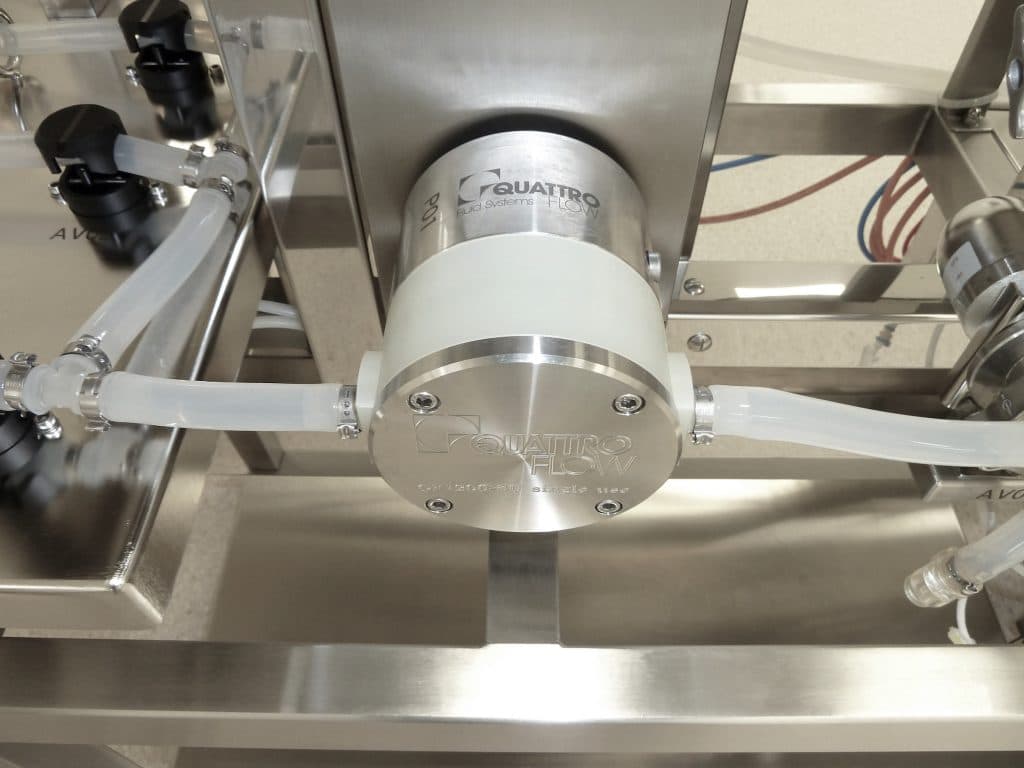
The breakthrough came last year with the development and release of the pump-chamber replacing system, namely the EZ-Set model that was created by Quattroflow™ Fluid Systems GmbH, Kamp-Lintfort, Germany, a product brand of PSG®, Oakbrook Terrace, IL, USA, a Dover company. The system essentially eliminates downtime in the production-changeover process, which leads to further optimization of the product-development timeline. It allows manufacturers to replace a single-use pump chamber in 30 seconds or less without the need of torque wrenches, or other special tools and equipment – all while allowing the user to be able to wear rubber gloves during the replacement process. Pump-chamber replacing systems can also be retrofitted on existing motor drives, which also makes upgrades quick and easy to perform.
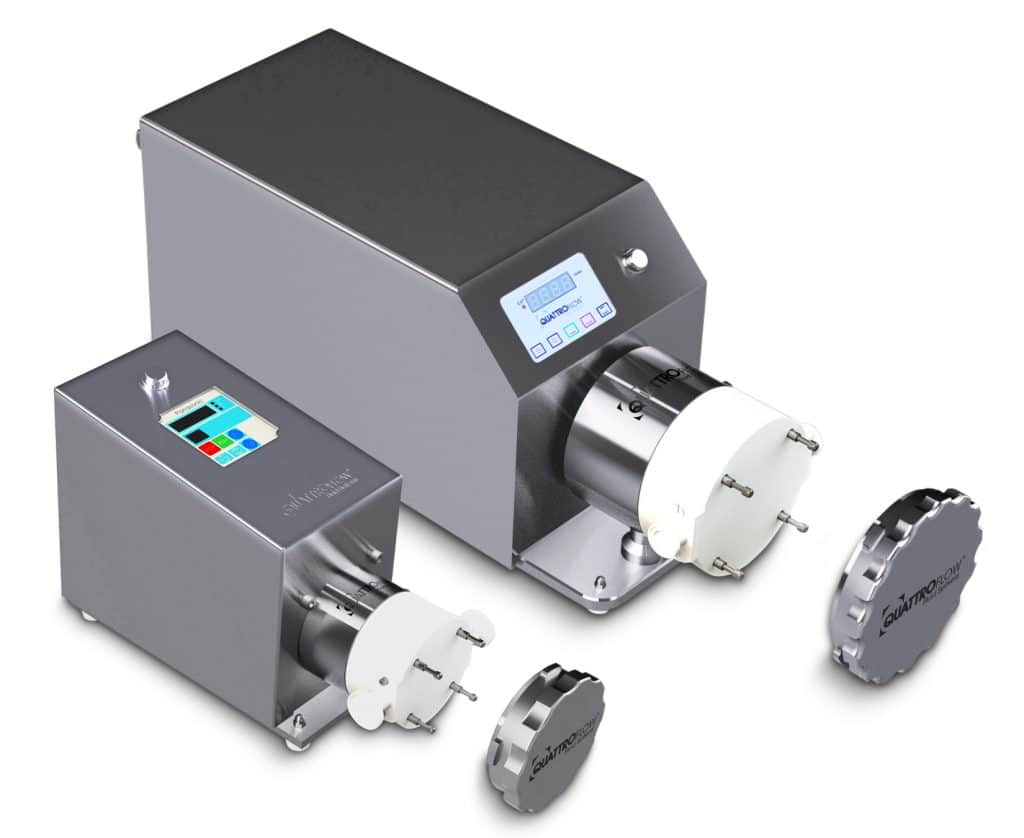
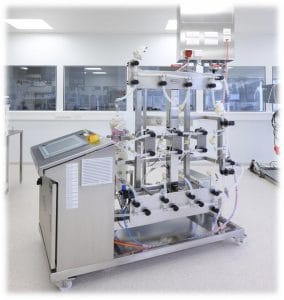
Replacing the pump chamber requires just five simple steps:
- Remove the pump’s pressure plate
- Take the pump chamber out of the ring drive
- Push the new pump chamber onto the ring drive
- Reinstall the pressure plate
- Slightly rotate the pressure plate to lock according to the markings
The markings on the side of the pressure plate, which show a minimum through maximum range, let the user know what the clamping force is since it is important to have the proper level of compression on the pump drive. In fact, the pressure plate is so simple and easy to dial in, that no physical strength is required, meaning that everyone from a kindergartner to a weightlifter can install the pressure plate.
Conclusion
Many skills are needed to produce biopharmaceuticals, but in the end the final product must be one that is unquestionably safe to use while simultaneously allowing the manufacturer to reap the financial benefits of an optimized patent window. The arrival of single-use pumps on the scene has virtually eliminated the cost and downtime that were previously required to clean and validate pumping systems. A further leap ahead has been taken, however, with the creation of the pump-chamber replacing system, an innovation that will continue to optimize time, cost, reliability and safety capabilities in the ultra-important biopharmaceutical-manufacturing industry.