What is Black Powder?
Black power is a name commonly associated with gas and hydrocarbon processing. It refers to abrasive particulates that are present in the process lines. Unlike the name suggests black powder can be seen in many colours from light brown through to black, the colour is largely dependent and the production field and the process.
Black powder is principally an iron based material, formed with iron oxides and iron sulfides. Varying amounts of dirt, can also be present, such as silica, calcium, chloride and sodium. Ultimately, black powder applications are generally ferrous or magnetic in nature.
In valve terms, black powder is mostly associated with processes in the Middle East, but in general terms it can occur through the production process, from the well, fluid separation and along the transmission lines. Once the refinement is complete, black powder can still be present in the downstream processes of both refineries and gas plants and then ultimately through to the end user.
Thinking specifically about transmission systems then the moisture that is often present can cause corrosion of the walls of carbon steel pipes. If H2S is present it can create corrosions in carbon steel components which ultimately can generate more black powder in refineries, process plants and storage systems.
There are measures for dealing with black powder but these are often expensive and involve a significant amounts of process down time. Chemical cleaners and pigging can be used in the pipeline, equally corrosion inhibitors can be used to limit the formation of black powder. Ultimately the user could use an alternative pipe material or pipe liner, such as plastic pipe or pipe with an internal lining.
What does this mean for the control valve?
As the majority of gas transmission systems are based on relatively soft carbon steels then the whole pipeline is susceptible to erosion due to the black powder. The amount of erosion will primarily be based on the flowrate (and hence the flow velocity) and the amount of black powder in the system.
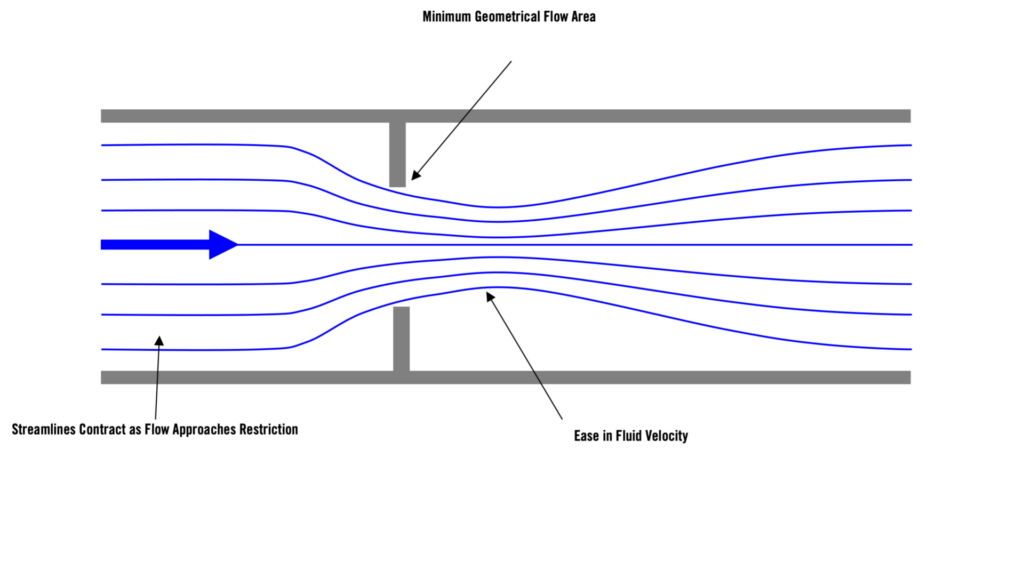
Although the black powder can impinge on bends or restrictions in the pipework geometrical area, control valves are generally the point where erosion is most likely. This is due to the fact that the very function of pressure reduction is caused by reducing the geometrical area of the pipe. This is normally done by the control valve which controls the flow area by the positioning of the valve plug. The net result of reducing the flow area is to increase the velocity of the fluid across the valve trim and hence, any particles in the fluid will impinge on material surfaces at a higher velocity ultimately causing erosion. This effect is shown on the simple diagram above.
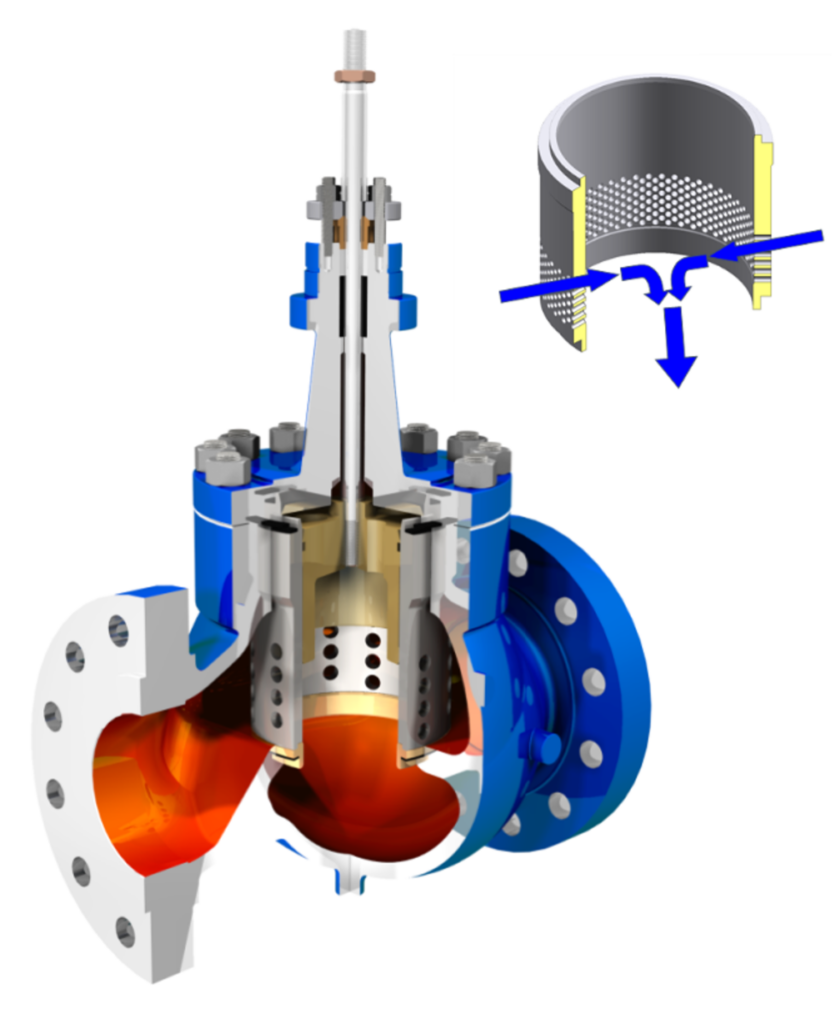
In gas transmission systems large size cage style globe control valves are generally specified to handle the volume of gas being transported. Often the line and valve sizes are 16” and above.
In a globe style control valve the gas pressure is regulated by modulating the position of the valve in a cage. Impingement of the fluid jets produces a more stable downstream flow, reduces the effect of large scale separation and produces a smaller scale turbulence structure in the valve outlet.
When used on black powder applications the control valve trim is therefore the point of maximum erosion due to the impingement of black powder.
In order to reduce the rate of erosion hard tungsten carbide is often specified.
Tungsten carbide is well known for its exceptional hardness and wear/erosion resistance. The addition of more ductile metals, as a binder (such as cobalt) greatly improves its toughness so that brittle fracture can be avoided. Cemented tungsten carbides are commercially one of the oldest and most successful powder metallurgy products. These composites are essentially aggregates of particles of tungsten carbide bonded with the binder metal via sintering. The properties of these materials are derived from those of the constituents – namely, the hard and brittle carbide and the softer, more ductile binder. The role of the binder in cemented carbides is to provide a ductile bonding matrix for tungsten carbide particles.
The tungsten carbide manufacturing process of tungsten carbide is such that the shape of the product is formed in the ‘green’ condition. In this condition the tungsten carbide is relatively soft and can be formed into the product shape. In the ‘green stage’ the tungsten carbide is approximately 50% larger than the final size. Once the initial shape is formed it is then hardened by sintering in an oven at high temperature. During the sintering process the component is both hardened and shrinks to its final size.
The large size valves on gas transmission systems dictate the requirement for large size valve trims and therefore large size tungsten carbide components. For tungsten carbide suppliers this often poses an issue due to the size of their ovens. In the majority of cases the number a carbide suppliers is limited due to their oven capacity.
Although exceptionally hard, tungsten carbide is also exceptionally brittle and care must be taken in the design and application of the carbide component. In control valves carbide is supported in steel retainers that are used to handle the compressive clamping loads of locating the trim in the valve. This means that the final stage of the manufacturing process is to shrink the tungsten carbide into the steel housing. To do this, the steel section of the trim is first machined to close tolerances; it is then heated so that the steel expands. Once at full expansion, the tungsten carbide can then be inserted into the steel, so that once the steel section trim cools and shrinks back to its normal size, then the components are locked together.
The process of assembling the tungsten carbide and the steel support is very difficult partly due to the size of the materials involved but mostly due to the speed required for assembly. For example, if the tungsten carbide is not inserted quickly enough the steel will have cooled in which case the parts will be locked together in the wrong position and effectively scrapped. Equally if engineering tolerances are not correctly specified or machined then this will potentially result in the cracking of the material.