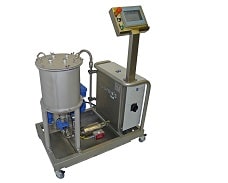
Our customer, a producer of silicon paste and gum, uses a test facility to develop new applications and materials, especially for their customers.
Their team of application engineers are available to support users that have problems in production. New solutions are also developed with this lab equipment.
Application
Continuous dosing silicones with viscosities ranging from 10,000 – 500,000 mPas into an extruder where the product will be mixed with polymers. Pulsations need to be avoided to guarantee the quality of the endproduct.
Problem
Until Suurmond was contacted, the customer had been using a reciprocating piston pump with limited viscosity capabilities. The quality of the end product was affected by the pulsating flow. Since the customer did not know any alternative (better) solutions, it was accepted as a fact: there is no other way to dose this product.
Significantly: the customer was not aware of any possible solution to
measure the flow of the highly viscous fluids, resulting in an inconsistent throughput. It was, therefore, impossible to maintain the desired accuracy of 1%.
Challenges
- Design a compact and easy to install dosing unit
- Including a tank, pump, flowmeter and control system
- Easy to connect to one of the ports of the extruder
- Mobile; quick installation and removal
- The unit must be able to dose and pump products with a wide variety of viscosities
- Limitation: NPSH
Our solution
A mobile unit, designed specifically to meet the restricted space available within the laboratory, that can be connected to the extruder with a hose and a 5 mtr power cord. The HMI was placed in such a way that the operator can easily access the unit from the operators panel for the lab extruder.
As the client wanted to measure the flow of the highly viscous media, a screw type volumetric flow meter was chosen. With this type of flowmeter the flow is measured via the PLC by monitoring the rotation speed of the screw.
Gear pump with conical inlet
For this unit we selected a Maag HYDROLUB® size 22/6 pump. Since this was not a pharmaceutical application, stainless steel was not necessary, the cast iron of the HYDROLUB® pump was compatible with the silicones used. Instead of a safety valve, which may be unreliable due to the high viscosity, the pump was protected by means of a pressure sensor. The base control system of the suurDOS® dosing system could be used, although extended with the pressure alarm and data- acquisition.
High pressure tank
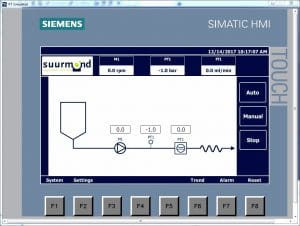
During the quotation phase of the project, it became clear that filling the pump would be a problem. To minimize the NPSH required, a pump was selected with a conical inlet; directly, vertically mounted underneath the tank. The outlet of the tank is the inlet of the pump. The tank was designed as an atmospheric tank, with the remark that for highly viscous media it might be necessary to pressurize the tank.
During the Factory Acceptance Tests, when two liquids were used with a viscosity of around 10 and 600 Pas, it was discovered that the high viscosity media did not flow into the pump sufficiently. High pressure was needed to get this product moving into the pump. As soon as it moves, the shear takes care of improved rheology and the pump is filled. Therefore, the customer decided to purchase a second tank, which could easily replace the original one due to the modular design.
The tanks have been designed for easy filling and cleaning. This was achieved by means of a novel split design.
Result
By using the dosing unit, the customer has achieved a continuous flow that can easily be set. The precision of better than 1% results in the improved quality of the tests and end-product. Users of the system are very enthusiastic about the intuitive operation of the system.
A special request from the customer was the possibility to use a mouse in case the touch panel became irresponsive. This could simply be realized by making the USB port, which is standard on the PLC screen, accessible from the housing. This became automatically a new standard for the suurDOS® systems.
“The name Suurmond equals a customized design with a high flexibility”.
Customer
It was further highly appreciated that Suurmond helped in the search for a solution that met both budget and requirements.
Side of this suurDOS® system
Front of this suurDOS® system