Removable Coatings for Flanges
Cortec® recommends two removable coatings for flange face protection. VpCI®-391 is a water-based temporary coating with low VOC (0.4 lbs/gal [48 g/L]). It leaves a clear non-tacky film that is virtually unnoticeable and can be easily removed with alkaline cleaners such as Cortec’s VpCI®-41x Series (which offers flash rust protection) before the pipe spool is installed. VpCI®-391 provides protection in harsh, outdoor, unsheltered applications and has excellent UV resistance. Since the coating leaves a dry film, it is ideal for transit applications where pipes and flanges may be repeatedly handled. For the most extreme conditions, VpCI®-368 offers even heavier duty protection. This fast-drying solvent-based coating leaves a slightly brown waxy finish and should be removed prior to flange installation using an alkaline cleaner from the VpCI®-41x Series.
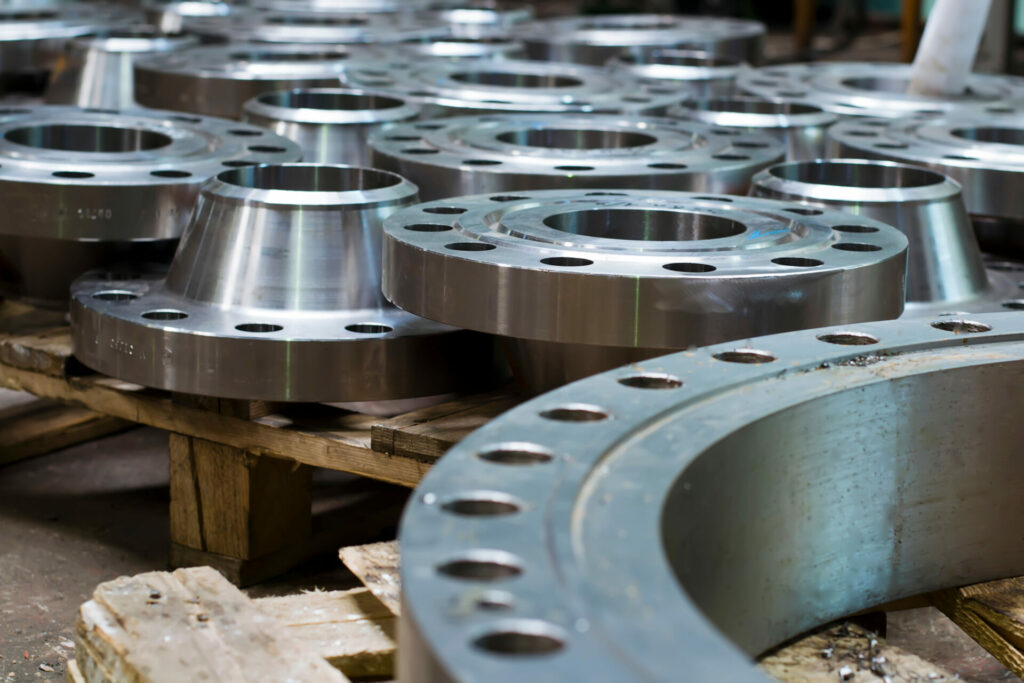
Removable Coating Advantages
As previously suggested, the main benefit of removable flange coatings is to avoid the ramifications of corrosion. Eric Uutala (Cortec® Technical Sales and Product Manager), who has extensive field experience with oil and gas industry preservation, explained the alternative: “If a raised face is damaged, either from corrosion or mechanical impact, it can cause significant delays in construction in startup activities. In the case of gramophone raised faces, the re-surfacing process can be very time consuming which could lead to further downtime (and money loss).” By taking the removable coating route, the protective mechanism conforms directly to the surface of the metal, not requiring an additional covering (e.g., plastic film) except what is needed for standard mechanical protection. In the case of VpCI®-391, there is minimal change to appearance—a plus for manufacturers concerned about aesthetics—and the coating is especially easy to remove for faster startup of the system.
Best Practices for Coating Flange Faces
Uutala reminds workers that flange preservation can be done at any point in the pipe life cycle—at the manufacturing plant, in the storage yard, or at the final site of operation. He outlines the flange coating process as follows:
- Make sure the flange face is clean and free of rust, dirt, coatings, and any other contaminants.
- Apply either VpCI®-368 (for brown, waxy film) or VpCI®-391 (for clear, dry film) by brush.
- Allow to dry for 1-2 hours (or more) before covering with rigid flange cover or other approved mechanical protection (avoid wood covers because they absorb moisture).
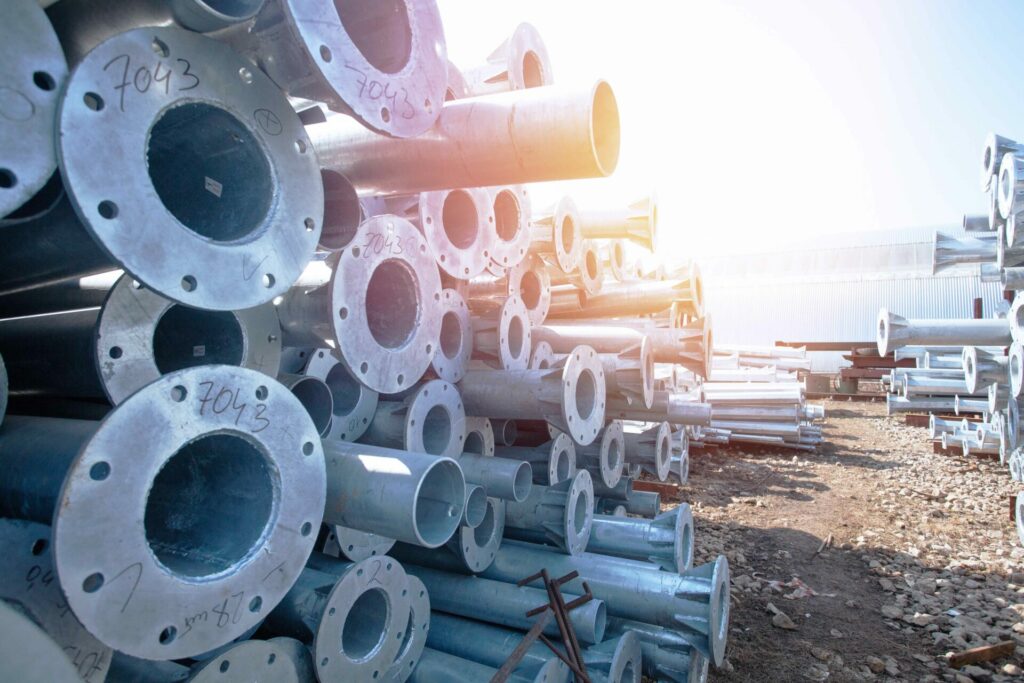
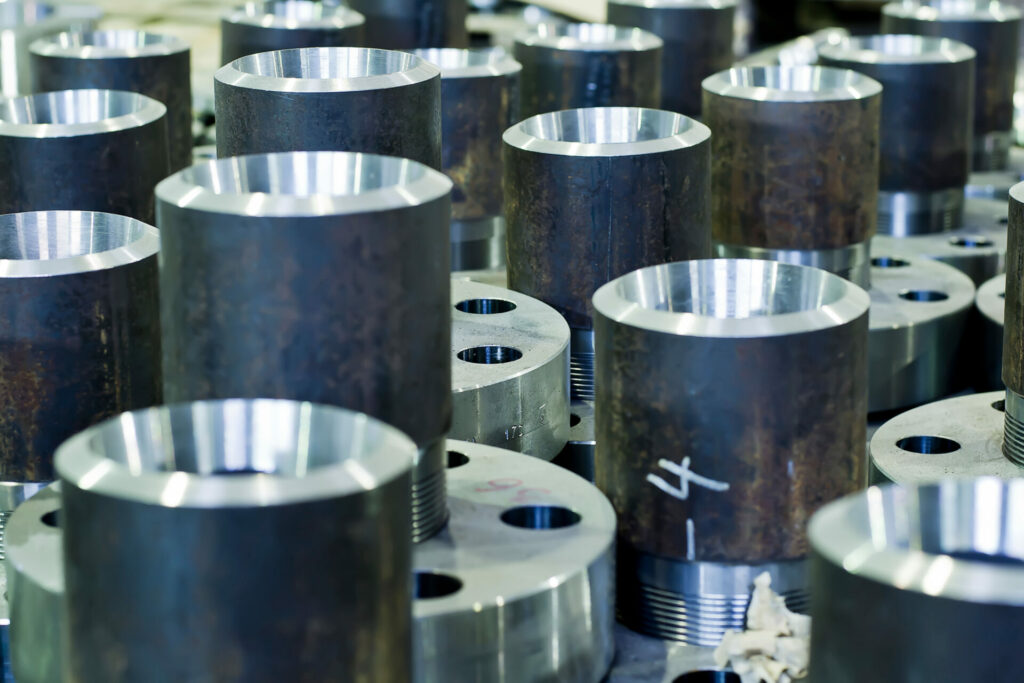
The Bottom Line
Ultimately, the condition of the flange face directly affects the condition of the system and is at risk at any point up to installation. Taking preventative measures to protect vulnerable flange faces from corrosion and mechanical damage during shipping and storage can go a long way toward preserving flange faces in their original state. A little time spent cleaning the flange and applying a coating now could translate into many hours and dollars saved later by avoiding resurfacing delays and minimizing system downtime. Contact Cortec® today to learn more about removable coatings for flange faces: