Processes such as corrosion, particulate build-up, and erosion can now be modeled using new software BOXERgeom. The software gives users the ability to apply simulation data to deform and generate new geometry.
The generated geometry can be meshed using BOXER’s meshing capability and analyzed to understand the performance of components during service and not pristine, manufactured conditions.
BOXER software is developed at Cambridge Flow Solutions Ltd.
“With BOXERgeom, we now can allow users to get a better idea of what is happening to components during service and how this affects their performance.” Bill Dawes, CEO of Cambridge Flow Solutions.
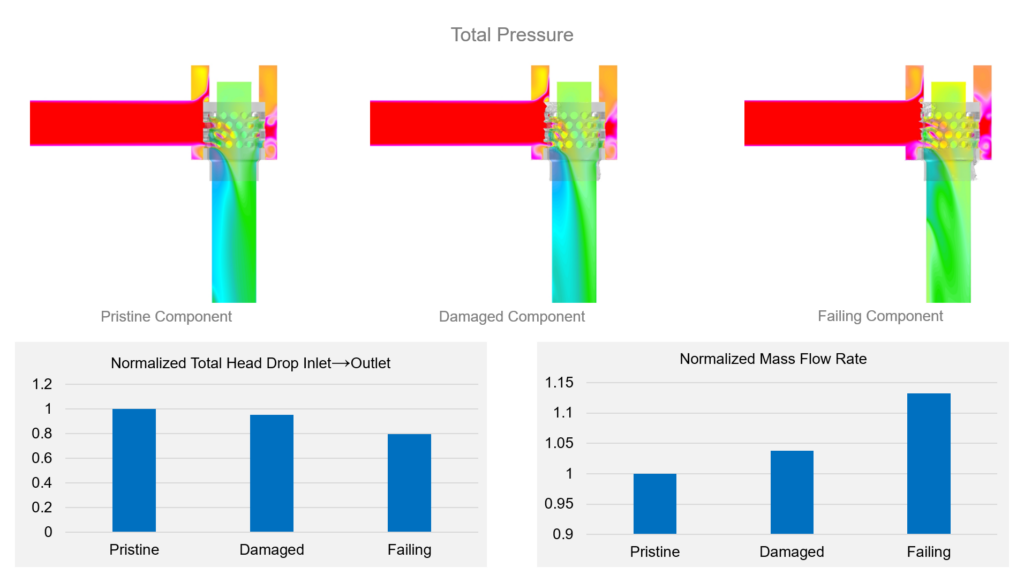
Choke Valve Erosion
BOXERgeom can alter a geometric surface in response to an arbitrary surface scalar value such as temperature, pressure, x-location, particle impact frequency, and erosion rate. The surface can be made to move outward (add material) or inward (remove material) to model particle build-up, icing, erosion, or burn-out in response to the local scalar value.
A Choke Valve can be susceptible to sand erosion in the Oil and Gas industry (reference). BOXERgeom’s unique tool enables users to model erosion on the component.
This capability enables users to:
- Create a digital twin
- Predict in-service performance of the component
- Predict component life span.
- Determine optimal operating conditions.
Using erosion rate data, material erosion may be modeled onto the geometry to create the geometry of the eroded component. The geometry may then be meshed within BOXER software for analysis.