The typical control valve is a globe valve with a screwed/welded in the seat, the plug guided on 1 place in the body or has an additional guide below the plug or in a cage and is operated with a single-acting diaphragm actuator that operates with air pressure on 1 side and springs on the other side.
For many applications this might do just fine, for applications where the bar is set higher because of the application or required availability there is another solution from Mascot: heavy-duty 1 piece plug & stem with double bonnet guiding with a double-acting piston actuator.
If you look at the pictures you already see some of the difference but let me explain in more detail.
A traditional control valve with a diaphragm actuator can have a screwed-in seat. These should be replaceable but in many cases, this will take some or a lot of effort. The threaded connection can be the start of a potential leak path. When the seat is welded in or seal welded after it is screwed in it’s more of what is already mentioned applies to replace it. The plug and seat need to be perfectly aligned otherwise there will be a bending force on the stem.
A clamped in seat has a seal between de seat and the body that is compressed until there is metal to metal contact between seat and body. This way there is no potential start of a leak path. The seat is held down by a cage that is held in place by the bonnet flange. Before the bonnet bolts are tightened the plug has centered the seat. This way there are no bending forces on the stem.
Heavy duty stem typically double the diameter of standard stem resulting in a bigger guiding surface. The bigger the surface the smaller the force on the guide which results in less wear. This will speak for itself, more area with the same force is a lower pressure resulting is less wear.
Heavy-duty stems don’t break. Vibrations can occur in a control valve, a stem with a smaller diameter will break quicker than a larger diameter. Again one that is quite obvious, more material to resist the forces is less chance of damage.
The plug and stem are 1 piece. Plugs that have come loose from the stem with a traditional control valve are not uncommon. When the disc is connected to the stem with tolerance to compensate for plug/seat misalignment this can be the start of a problem as vibrations can have serious damage as result.
Easy maintenance, loosen the bonnet and the seat ring can be replaced without any further tools as it is only clamped in. Does the process change and the Cv value needs to be changed, easily replace the plug & seat. This is not as easy when the seat is screwed in or seal welded.
A Piston actuator only has 1/3 of parts compared to a diaphragm actuator. Easier maintenance, less inventory. 1.000.000 cycles is quite normal for a piston actuator
A piston actuator has 1/10 of the operational cost compared to diaphragm actuator. Only a few O-rings are the normal replacement parts.
Easily reversable, disassemble the actuator and place the spring at the other side of the actuator. It’s just 1 spring.
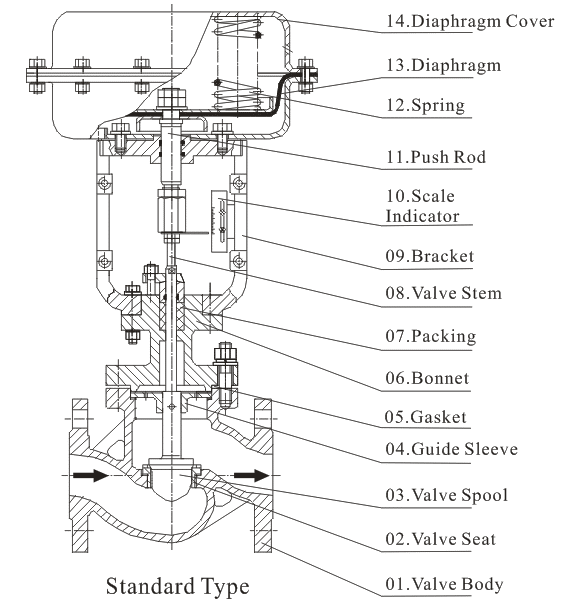
High stiffness, good repeatability low hysteresis. A diaphragm actuator has a relatively large volume compared to a piston actuator. Air is compressible, more air result in bigger differences. Air can permeate through the diaphragm, 3 % on average, typically with older ones but it means the position is not maintained without adding air. The diaphragm is susceptible to aging which will make it less flexible and it will respond less linear, this will be seen in accuracy.
A piston actuator is compact (space saving) and light weight, typically diaphragm actuators are bigger and heavier. Especially with bigger valves this is significant.
The spring in a piston actuator is just for fail safe as for normal operation air is used on both sides, a diaphragm actuator is dependent on spring to close or open the valve based on the fail action.
Higher speeds / faster stroking is possible with piston actuators than diaphragm actuators. The 1st reason is the lower volume in the piston actuator. The 2nd is that a piston actuator is operated on both sides of the piston with compressed air where 1 side is supported by the spring. A diaphragm actuator only has air on 1 side.
Piston actuators can handle up to 10 bar supply air possible, so smaller actuator possible if constantly available..
So a technically strong design that cost less to maintain, requires less maintenance, provides better control so a better product from the process and has a higher availability and shorter downtime. This results in a cheaper valve if you consider cost of ownership of the valve and better operational results.