A major obstacle Petrobel faced was the common problem of hydrates, which are ice-like solids that form when water and gas combine and crystallize in a high-temperature, low-pressure environment. The formation of hydrates in oil and gas pipelines causes reduced capacity and eventually a complete blockage which may rupture the pipeline.
Pulling the plug on hydrate formation
Locating and removing these hydrate ‘plugs’ – which can be hundreds of metres long – is difficult and carries significant remedial costs along with loss of production and revenue; therefore prevention is essential.
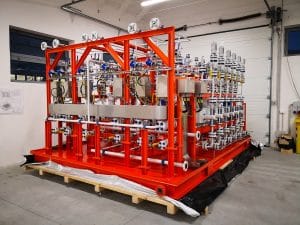
The operator’s preferred method of hydrate inhibition was to inject glycol into pipework in order to adjust the thermodynamic conditions that allow hydrates to form. For this they approached SEKO, a global leader in metering pump design and manufacture, to supply its products as part of a glycol injection package.
“Nexa Series pumps were selected for their flexible configuration, superior dosing accuracy and excellent reliability”
Following a comprehensive assessment of the process between SEKO and Petrobel, it was decided to use 12 Nexa Series packed plunger dosing pumps with multi-head setup for glycol dosing. These were mounted on a large rig that could be transported as a complete unit to a fixed offshore platform ready for installation.
Nexa Series pumps were selected for their flexible configuration, superior dosing accuracy and excellent reliability, representing the best solution to cope with the harsh environmental conditions and fluctuating temperatures encountered in oil and gas applications.
Nexa features
- PTFE diaphragm for outstanding chemical compatibility
- ATEX approved for explosive atmospheres
- Multiple head execution with different mechanism size and gear ratio
- Design meets and exceeds API 675
- Flow rate up to 7,500 l/h
- Pressure up to 660 bar
- Fluid temperature -10°C to 90°C (-40°C to 150°C on request)
- Manual and automatic flow-rate adjustment
- Zero-leakage profile
- Multiple mounting options
This installation means Petrobel can carry out its operations without concern over hydrate formation and its associated costs, helping to increase profitability while reducing maintenance requirement.
Another example of a SEKO solution helping customers achieve long-term, cost-effective improvements in their daily operations.