The customer, a subsidiary of a multi-billion-euro gas utility, stores natural gas underground in order to offer a strategic reserve that helps suppliers:
- Maintain supply in the event of disruption to production or transmission
- Supplement pipeline supply during daily and seasonal peaks
- Conserve excess gas that may otherwise be wasted or flared during periods of low demand
The operator’s chosen method of storage is to inject gas into the porous rock of depleted reservoirs, which are empty natural repositories already exhausted of their recoverable gas. As well as providing the same conditions that safely maintained the gas for millions of years, this technique ensures further environmental disruption is avoided.
Overcoming a potentially-catastrophic threat
One of the challenges faced by the operator is the formation of hydrates in equipment and piping from the reservoir head to the treatment plant. Hydrates are ice-like solids that form when water and gas combine and crystallize, and in natural gas transmission and storage they cause reduced capacity and over time will block and possibly rupture the pipeline.
In order to prevent the formation of hydrates, the operator wished to inject methanol into the gas and commissioned SEKO to supply metering pumps for installation in the first-phase treatment plant.
With a brief to supply industrial process pumps capable of operating within an ATEX-classified area and dose methanol at 30 litres per hour at 86-bar pressure, SEKO specified its Nexa API 675 metering pump as an ideal solution.
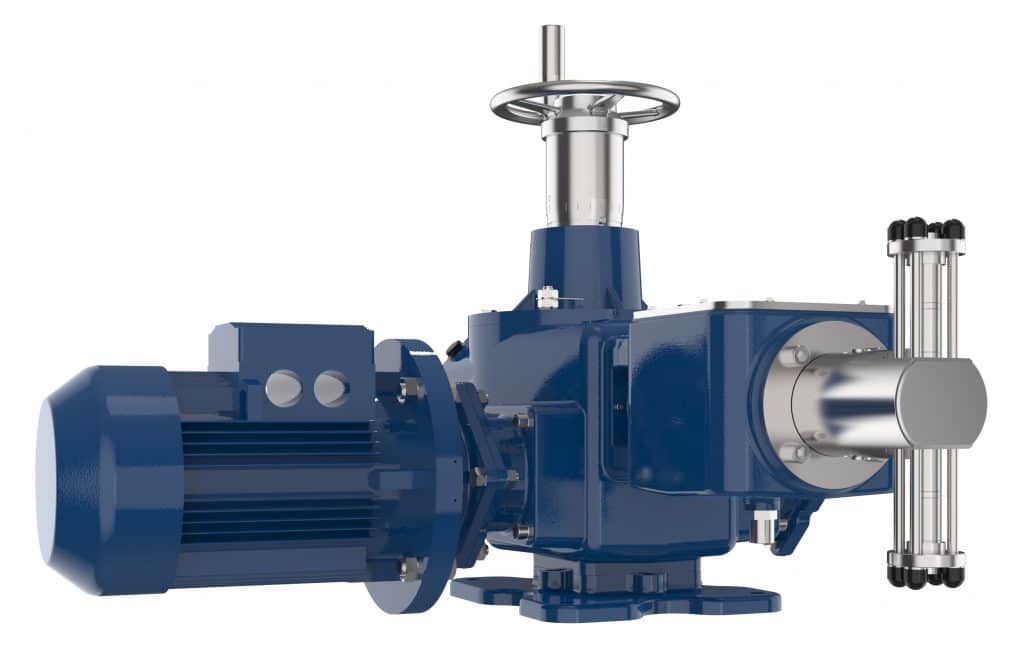
Combining high performance with outstanding durability
The Nexa’s quality finish, wetted parts in 316L stainless steel and ANSI-standard flanges offered outstanding chemical compatibility and durability which was essential in such a demanding heavy-industrial process.
This robustness was complemented by Nexa’s ATEX rating for use in potentially-explosive atmospheres – a non-negotiable element of the client’s design specification.
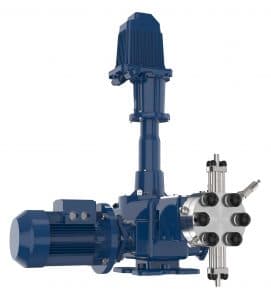
Meanwhile, the pump offered the flexibility of vertical or horizontal motor mounting and its modularity would allow the system to be easily extended in the future.
By avoiding the threat of hydrate formation in pipework and equipment, the operator could ensure its process performed at maximum efficiency, which would also deliver the environmental benefits of reduced gas flaring.
Another example of a SEKO solution helping customers achieve long-term, cost-effective improvements in their daily operations.
Nexa features & specification
- Capacity range up to 7800 l/h with single head
- Flow-rate adjustment: manual, electrical 4-20 mA, pneumatic 3-15 psig and/or SMART (protocol HART) servomotor and/or by frequency converter drives
- Adjustable seal provided for flushing or leakage recovery
- Multiple head execution with different mechanism size and gear ratio
- Operating pressure: up to 350 barg (hydraulic diaphragm) and 650 (plunger diaphragm) with higher pressures on request
- Wetted parts SS 316L, PP, PVDF, PTFE. Special configurations available upon request
- Multiple head execution with different mechanism size and gear ratio
- Motor positioning: vertical or horizontal
- Flow rate: up to 655 l/h
- Compliance with API 675
- Certified to ATEX 2014/34/EU