Over the past few decades, the Iris® diaphragm control valve has proved its worth in hundreds of wastewater treatment plants, where it is used primarily as a flow control valve to ensure economical input of air into the aeration basins.
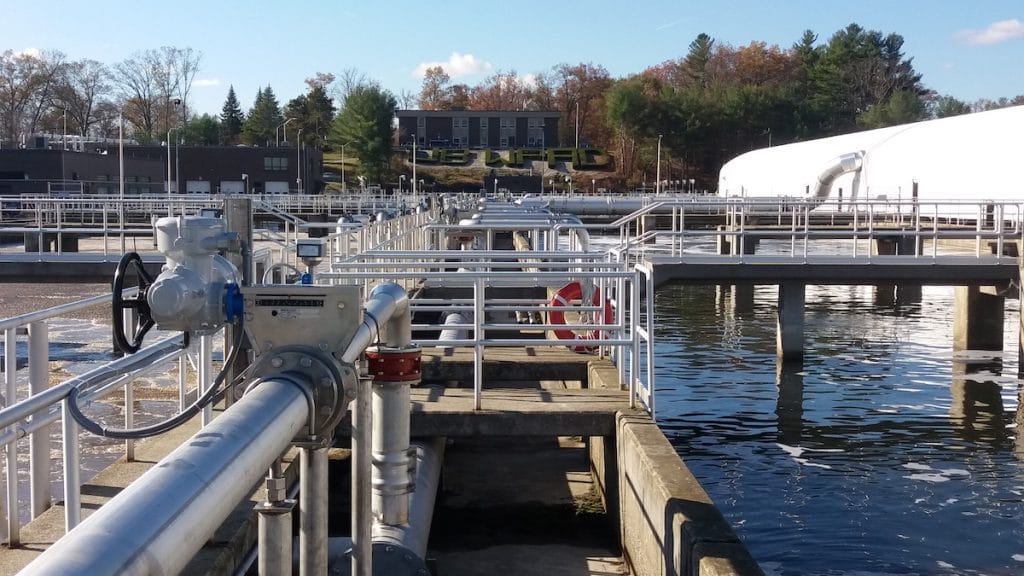
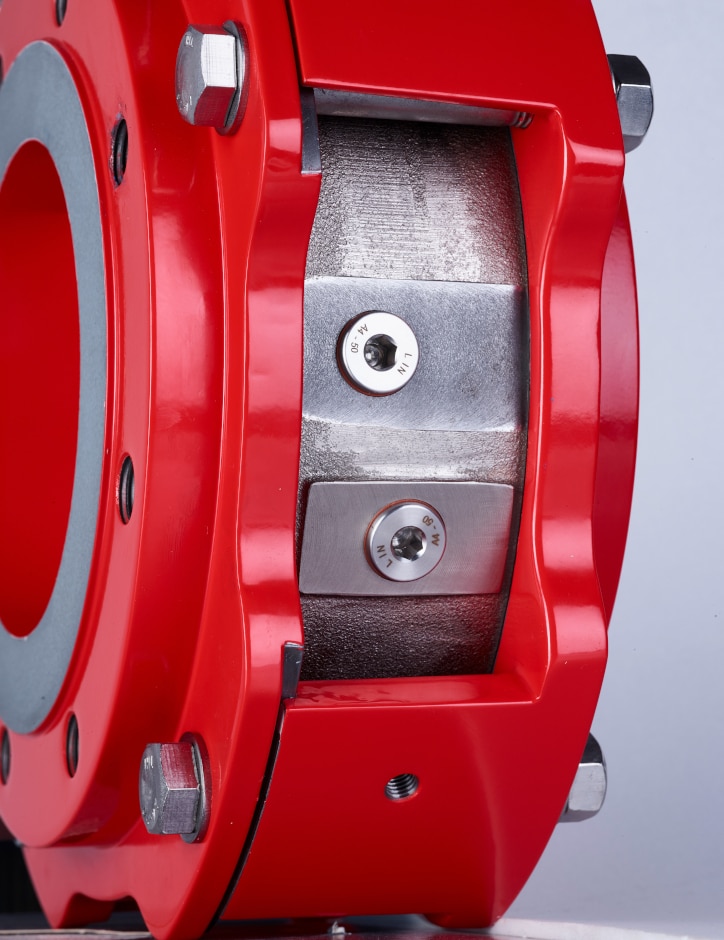
In 1958, the Iris diaphragm valve was developed by the company’s founder, Emile Egger, and launched on the market, where it was used primarily for paper pulp control in paper factories.
At the beginning of the 1980s, Egger introduced an updated version. Iris diaphragm control valves have been used mainly in aeration basins in wastewater treatment plants ever since.
Thanks to its unique design, air quantities can be regulated precisely and reproducibly. This enables the operation of stable biological processes and the implementation of, and precise adherence to, extremely low oxygen input values. This in turn results in high energy efficiency and the high stability of the entire activated sludge process.
The company is driven by a desire to make the tried and tested increasingly better. Thanks to systematic further development, Egger is proud to launch a completely redesigned and technically revised Iris diaphragm control valve onto the market; the company has named the new model generation “IBS”.
The new IBS
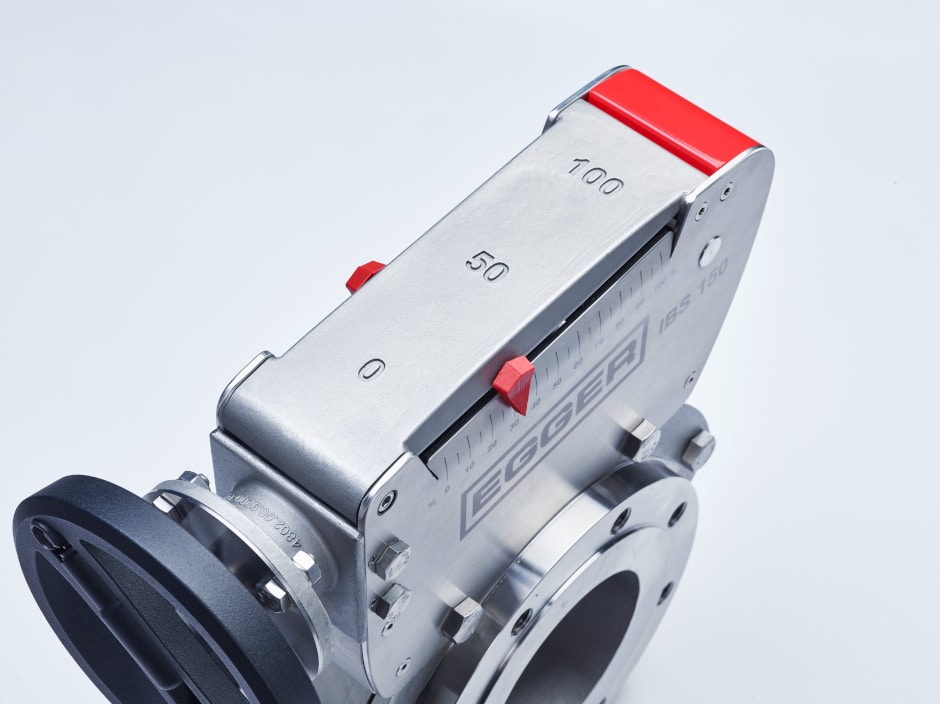
The modern industrial design and compact structure with shorter installation lengths are immediately visible. It is advantageous for a plant operator to know the position in which a control valve is located. As a result of this, the visual position indicator has been completely revised and is clearly visible from three sides even from a long distance; this is in addition to the electronic feedback of the variable speed drive position to the SCADA system.
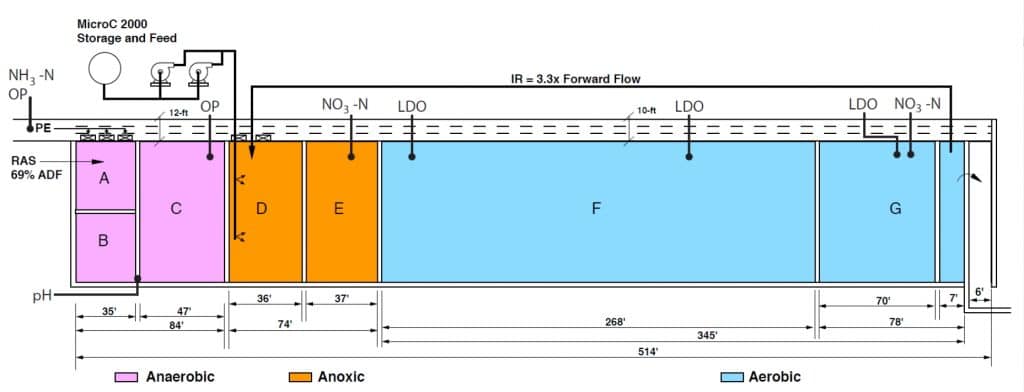
As an all-rounder, the new IBS can be used in a number of industrial applications; its gas-tight design without spindle feedthrough opens up many new possible applications for regulating chemicals and industrial gases. The Iris gate valve is also prepared for monitoring systems and can be pressurised and equipped with gas or liquid flushing. Leak tightness monitoring and flushing systems can be connected (or added) without changing the design.
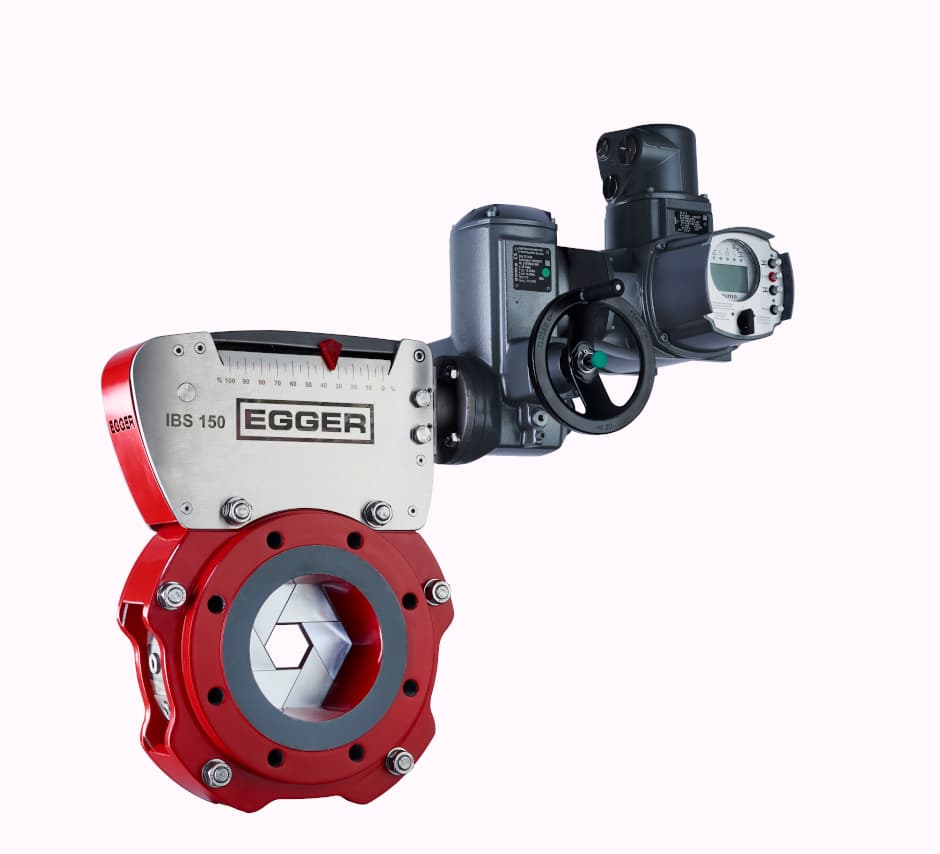
Its robust design and self-cleaning segments also make the valve a reliable regulator for raw sewage or sludge. Iris diaphragm control valves are therefore used to control raw sewage, process water, primary and aerated sludge, and also for the task of loading centrifuges with digesting sludge.
The three buffer liquid and flushing connections of the new IBS are offset by 90° and can also be used for drainage and emptying condensate, which is a major advantage for plants that are shut down periodically.
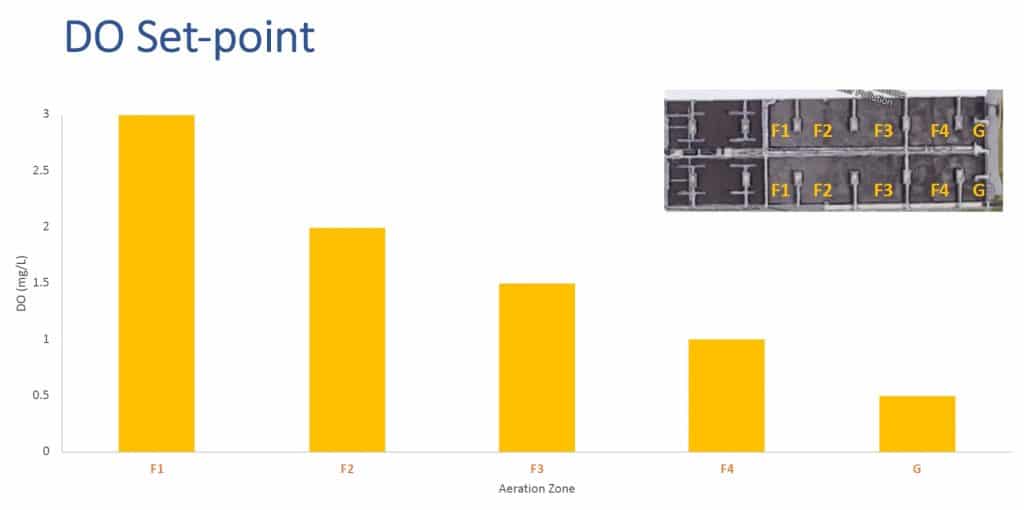
The self-locking spindle nut design of the IBS enables maintenance-free and cost-extensive operation, thus simplifying the use of the control valve in inaccessible locations. An additional advantage for the operator is the ability to replace the drive support or parts thereof without having to remove the Iris valve from the pipe line.
Economical and precise regulation of aeration air at Upper Blackstone Waste Water Treatment Plant
Iris diaphragm control valves enable the stable and repeatable regulation of media over the entire valve stroke. For gases and aeration air, the Iris gate valves are designed so that the quantity to be regulated can be operated within a high control-accuracy range without hysteresis.
Its unique design with six centrally opening segments which can be retracted completely into the casing results in an equal-percentage valve characteristic for the Iris valve. This leads to a virtually linear operating characteristic curve with a large control range, enabling the operation of economical control loops. The differences in the operation of control valves and Iris diaphragm control valves can be briefly explained using the example of the Upper Blackstone wastewater treatment plant in Massachusetts, US.
Complete renewal of the wastewater treatment plant’s biology took place in 2018, including replacement of the existing butterfly control valves, blower technology and diaphragm aerators. Besides process optimisation, the objectives of this major conversion project included energy savings when ventilating the aeration basins. With an average throughput of 30 mega gallons/day, hydraulically corresponding to a 670,000 population equivalent, the plant consists of four aeration lines with seven control valves each.
During the conversion measures, the manually operated butterfly control valves were replaced with Iris diaphragm control valves in order to enable precise oxygen input into the basins with the aid of a most open valve strategy
(MOV) and thus reduce energy costs. Upstream of the control valve, each aeration zone was equipped with an ABB Sensyflow type mass flow meter in order to control the Iris valves using the actual flow volume and operate them in the most open position possible.
Striking improvements were realised after just a few weeks of operation thanks to a MOV with the Iris valves.
The required oxygen contents for the various basin zones were adhered to very precisely without tuning with minimal fluctuations around the O2 setpoint value (see Figure 6 for the results and achievement).
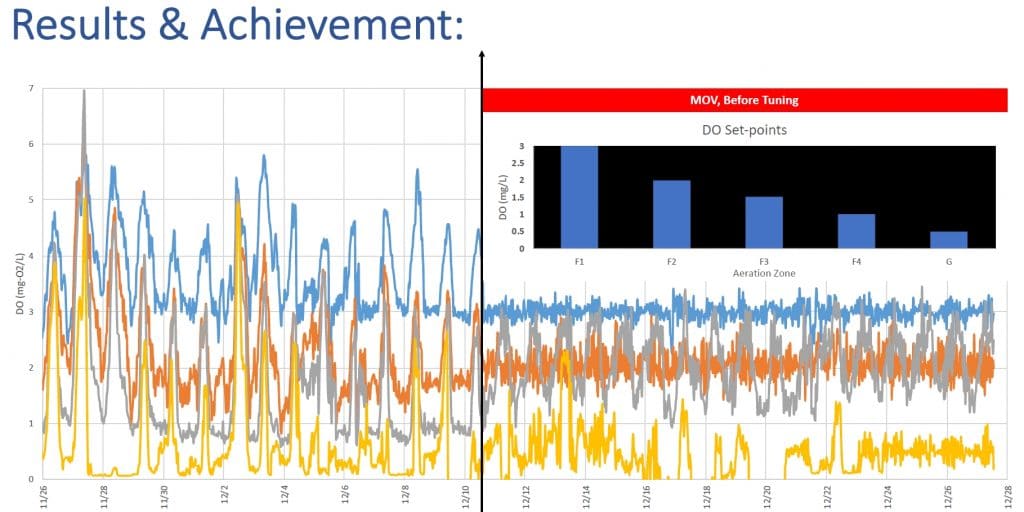
At the beginning of 2019, the MOV strategy was further optimised using Iris valves; the results are self-explanatory:
Figure 7 shows the high control accuracy of the Iris diaphragm control valves; the actually achieved O2 values only fluctuate slightly around the set point value with a constantly changing air volume input depending on the current dirt load at the wastewater treatment plant. The air volumes are shown in the lower half of the diagram in ‘standard cubic feet per minute’.

This highly precise control philosophy and the new machine technology enabled significant amounts of energy to be saved, as a comparison of the plant’s daily energy requirements between 2016, 2017 and 2019 shown in Figure 8. The energy consumption could be reduced by 10% on average, as shown on the red graph from 2019 (operation with Iris diaphragm control valves). The discharge values were also significantly improved and the use of additional chemicals such as carbon was extensively reduced.
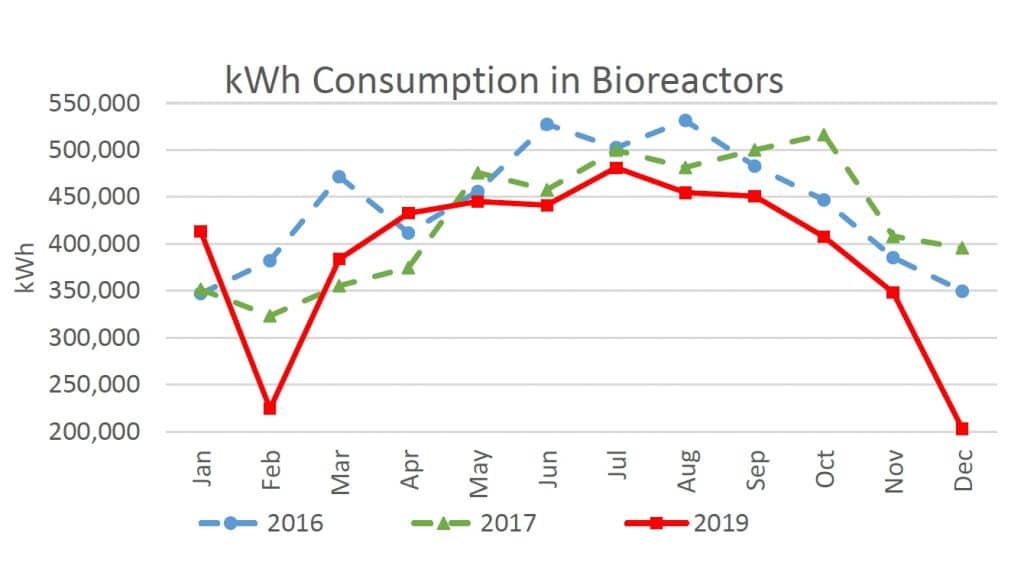