According to the Center for Climate and Energy Solutions (C2ES), tropical storms have become more common in North America since around 2000. Frequency and intensity vary from basin to basin. In the North Atlantic Basin, the long-term (1966-2009) average number of tropical storms was about 11 annually, with about six becoming hurricanes. More recently (2000-2014), the average is over 15 tropical storms per year, including about seven hurricanes. This increase in frequency is correlated with the rise in North Atlantic sea surface temperatures, which could be partially related to global warming. Hurricanes and Climate Change |
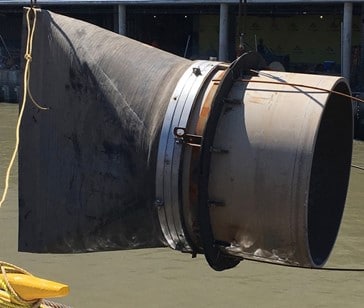
Natural disasters remind us of the unpredictability we all face on a daily basis—but on a grander scale. Weather events especially can cause large amounts of damage with little warning and in extremely short periods of time. But their reach isn’t over when the storm passes. Lots of property damage and even health and safety threats continue in the hours, days, and weeks after natural disasters. This is true whether it’s a hurricane, a tornado, a flood, or another dangerous storm system.
The best way to minimize this damage is to prepare ahead of time. For most individuals and municipalities, it’s not a question of if—but when—systems will be tested by a storm.
It’s everyone’s responsibility to prepare for these storms. For municipalities and other local governments, this means making sure infrastructure is up to date and designed to handle extreme conditions. A failure of stormwater or wastewater systems during a hurricane can take a problem from bad to worse.
In a natural disaster, stormwater drainage system components can struggle to keep up with demand. Ideally, the system would continue to drain the influx of water. But even if the system can’t work fast enough, preventing backflow is essential.
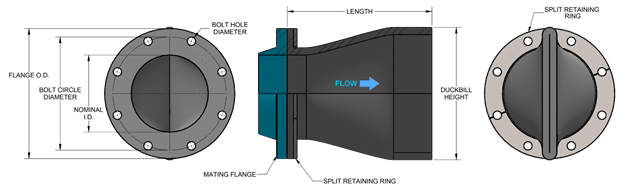
The Dangers of Backflow
Backflow is a condition in which the fluid in a system moves backward— flowing back toward the source. Of course, backflow means the system isn’t operating as designed. It’s never a word that operators want to hear.
But backflow is most dangerous in applications that involve harsh chemicals, sewage, or other hazardous fluids. Having these fluids move in a way that the system wasn’t designed to accommodate can lead to all kinds of issues. For example, stormwater that’s mixed with other system fluids could end up coming back out of storm drains and into the street. Backflow in these situations can contribute to flooding, standing water, and contaminated water exposure for citizens in residential areas.
Stormwater management isn’t the only application in which backflow is a dangerous condition. For example, some systems are at risk of causing land erosion if a system failure leads to backflow. Or when dealing with other infrastructure systems, saltwater could end up in a freshwater pond. All of these risks demonstrate why preventing backflow should be a priority during system design.
The Importance of Check Valves
The check valve is a crucial system component for preventing backflow. Check valves help a system maintain one-way flow. They open based on the pressure of the fluid flowing through the system, then close to prevent the fluid from flowing back toward the system inlet.
Check valves are often overlooked because some system designers believe these nonmechanical, fully passive devices are simple, and when the best check valve is installed in a particular application or system, their dependable operation can make them seem simple. These very low- to no-maintenance, long-lasting devices quietly do their job. Once they’re installed, they can fade into the background and do their part to keep a system running for years.
But an improperly selected check valve can be a major headache. A design that’s mismatched for the application can lead to the valve being stuck in an open position. A material that doesn’t work well with the system fluid can lead to rust or corrosion, requiring frequent maintenance or replacement. And some selection errors can even lead to loud and dangerous water hammers, putting other system components at risk.
Rubber Check Valve Advantages
Using rubber check valves helps avoid a variety of common issues with check valves of the past. Metal check valves seem like they would be durable and long-lasting, and they often are. But depending on the fluid, metal materials can have a lot of vulnerabilities as well. For example, saltwater that finds its way into a local stormwater or wastewater system can be highly corrosive to metal components. More common fluids like raw sewage can be too corrosive for many metals.
In addition, metal check valves often struggle to handle slurries with large amounts of solids. Of course, solid-handling capability is critical in wastewater applications. It’s also important in stormwater systems where the pumped fluid often hasn’t been through much processing before reaching the check valve. In both of these situations, rubber check valves offer a great solution.
The advanced elastomers that makeup Proco’s rubber check valves are specifically designed to work in these applications. They allow users to design a system to prevent backflow without the maintenance headaches of other check valves.
Rubber check valves can withstand harsh, erosive fluids without rusting or deteriorating. For example, the elastomers used in the Series 700 ProFlex™ Rubber Check Valves from Proco Products, Inc., are designed for these applications.
Special Circumstances for Rubber Check Valves
Operators can consult with an expert at Proco Products, Inc., on how to choose the correct check valve for their system. These valves are designed to be long-lasting and require no maintenance, automation, or manual assistance to operate. They’re often installed in hard-to-access locations— underwater where only divers can access them, for instance. In those situations, it’s important to get the right valve in place from the start.
If the valve will be installed in a submerged condition, it’s critical to choose a check valve that’s designed for that situation. Rubber is often a great choice for these conditions since it’s resistant to many types of wear. The valve can stay installed and continuously operate without requiring expensive, inconvenient maintenance or assistance.
Rubber check valves are also a great choice when dealing with a very high flow application. The elastomer often absorbs energy from the fluid much better than a metal check valve would. This can lead to quieter operation, which is critical if it’s being installed in a residential area.
In any system, maintenance is a major consideration for every single component. When a user chooses an elastomer check valve, maintenance can be left off the checklist. There’s nothing to lubricate and no need to perform any regular or preventative maintenance. The valves operate continuously without intervention. Another condition that might indicate a rubber check valve would be a system handling fluids at a very high or low temperature. The specialized elastomers used in Proco’s check valves can handle fluids ranging from -65 F to 400 F. This low maintenance component offers great peace of mind when users are designing or operating a system for a tough thermal application.
Conclusion
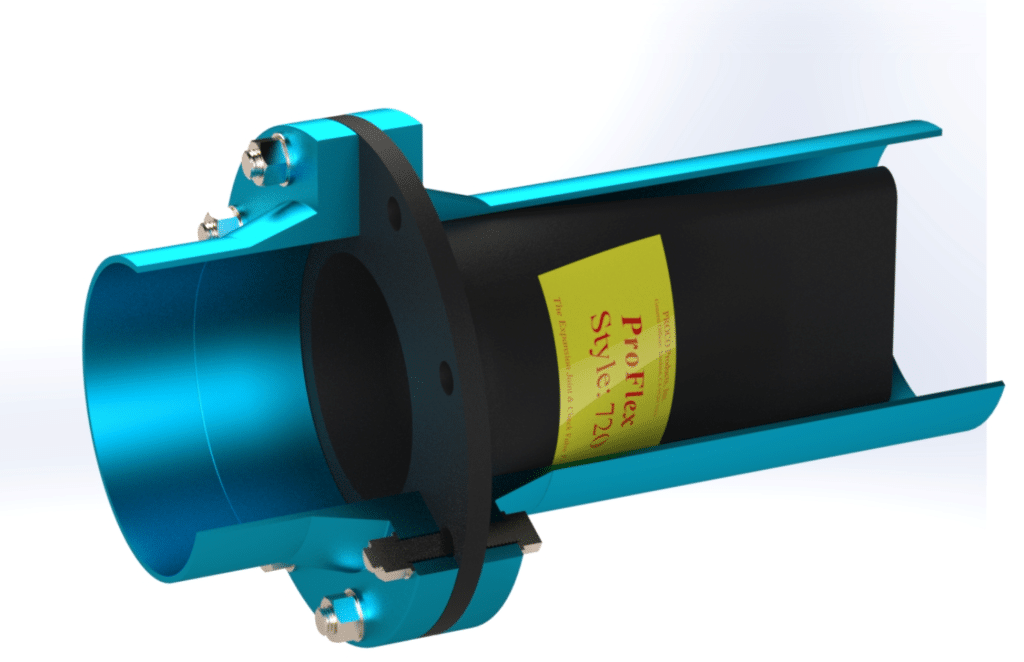
When reliability is the goal, check valves are excellent tools for system designers and operators. Keeping fluid moving in the correct direction, even when a water management system is outside of ideal conditions, can prevent some of the most dangerous effects of major storms. Rubber check valves, when selected and installed properly, make important contributions toward system reliability—even when extreme weather puts systems to the test.