Based on its 20 years of experience with the Direct In-line Pumping DIP systems, SIDE Industrie developed the DIP-Booster to manage excess stormwater flows. When a pipe becomes overloaded during a major rainfall or similar overflow event, the DIP-Booster starts automatically and can double the flow of a simple gravity fed line.
Manny Possible Applications
With climatic phenomena becoming exceedingly unpredictable and storms becoming increasingly violent, the existing storage facilities, such as stormwater basins, are not always sufficient. The DIP-Booster allows for increased flow rates without replacing the entire existing pipe and can be used for gravity-fed lines with diameters ranging from 125mm to 1200mm (5’’ to 48‘’).
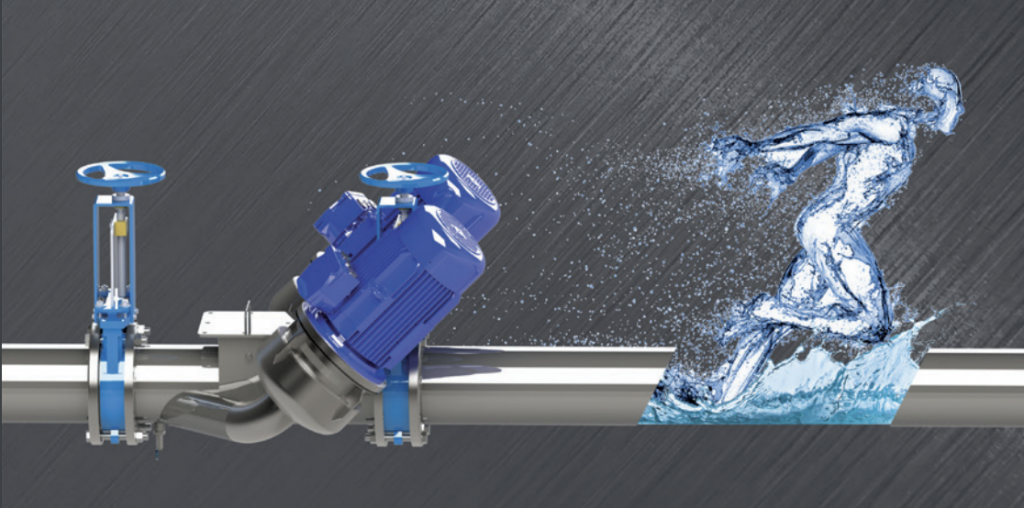
This system can be used to solve many problems:
- pipes with insufficient slope or counter-sloped pipes
- pipes undergoing periodic backups
- accelerated in-line wastewater circulation
- insufficient flow of a gravity-fed line due to inadequate pipe slope
- overpressure of existing discharge
The main advantage of the DIP-Booster is undoubtedly to avoid the oversizing of traditional equipment. It offers an economical and reliable alternative solution for flood protection with the following benefits:
- savings by using smaller pipe diameters
- reduction of retention time
- increased scouring when needed
- circulation between basins
- increased discharge pressure when needed due to downstream flooding
Operation and Characteristics
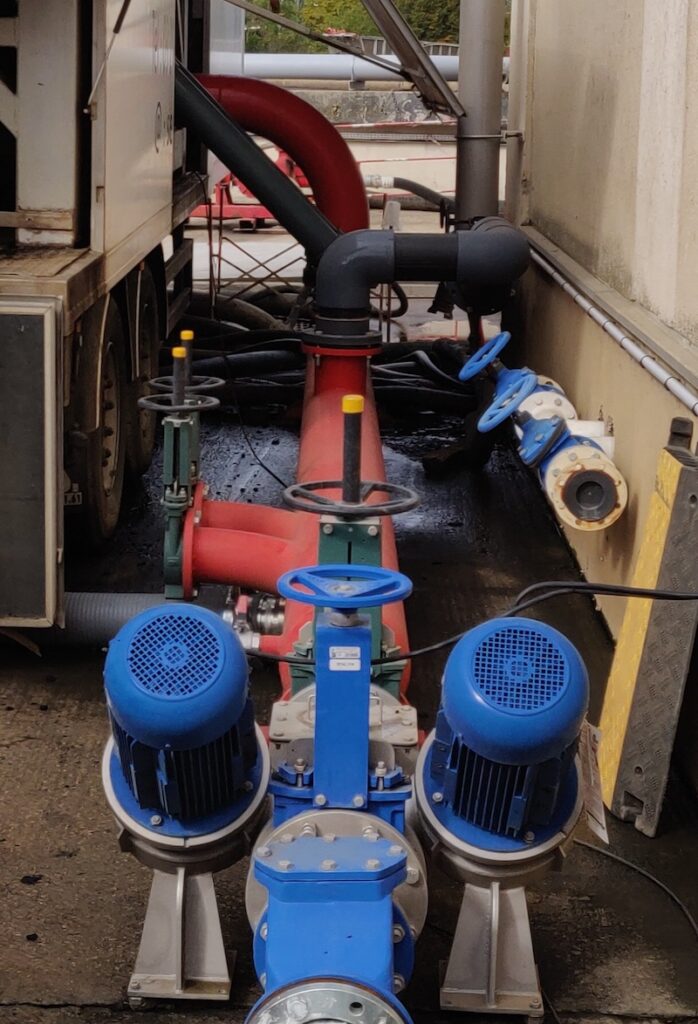
The effluent flows through the DIP-Booster by gravity as long as the pipe is not filled. The motors are switched off, the control panel leaves them in standby and continuously checks the level via the level sensor. The internal valve is open. When the water level rises, the gravity flow fills the pipe and the DIP-Booster’s body until the start-up level of the first unit is reached. The motor will start slowly and accelerate the flow. The flow will then close the internal check valve. The second unit starts if the upstream level continues to increase. The motors slow down and then stop as the upstream flow decreases back down to normal gravity flow.
All the elements constituting the common hydraulic body are made of stainless steel AISI 304L or 316L. The shafts are sealed by mechanical seals made of suitable materials. The motors are IP67 TEFC and designed for continuous operation during regulation phases, and for intermittent operation, up to 150 starts per hour, in the low flow phases. The DIPCut impellers operate as conical vortex impellers in the normal pumping phase and become “shredders” in the automatic reverse unclogging phase.
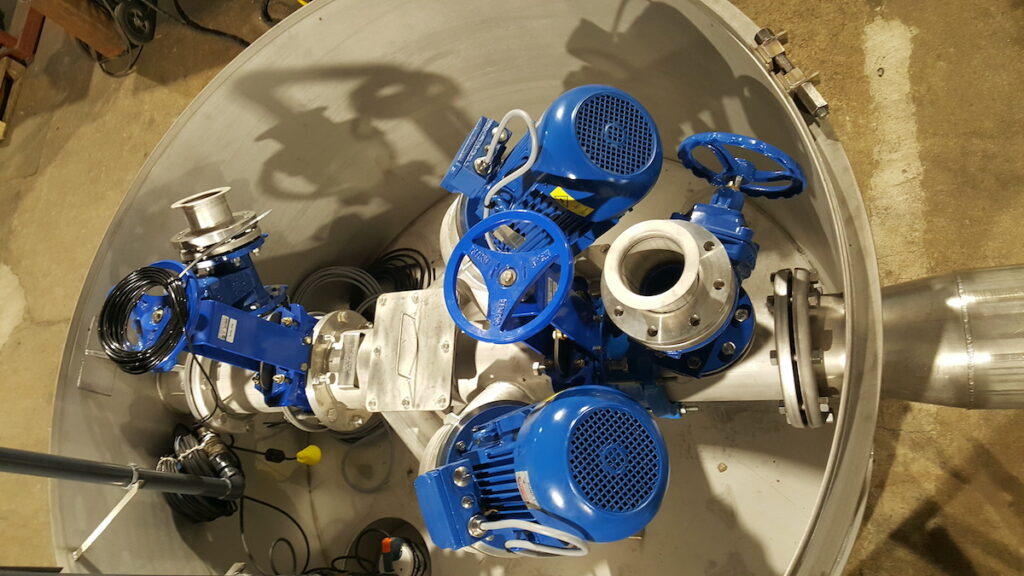
* DIP brand is available under the name OW (OverWatch) in the US and manufactured by IFS (Industrial Flow Solutions).