Requirement
Commissioned in the early 1900s, the Texas Gulf Coast refinery produces gasoline before oxygenate blending, diesel and jet fuel, petrochemicals, petroleum coke and sulfur. The customer required a reliable zero-leakage valve that would offer repeatable and reliable shut-off so instrumentation could be maintained and calibrated while the unit was online.
In addition to ANSI standards, A217 C12 material specific limits on vanadium and aluminum were required. These key elements extend the life of the equipment, ensuring continuous operation of the plant.
Solution
ValvTechnologies designed and supplied six 2” 300# Class and more than 40, 2” 600# Class V1-2 series ball valves to satisfy the customers requirements. All valves were A217 C12 raised face flanged end, gear operated and installed in the plant’s wedge meter assemly. The valves will provide positive isolation to the instrumentation allowing the unit equipment to be maintained on-line.
Result
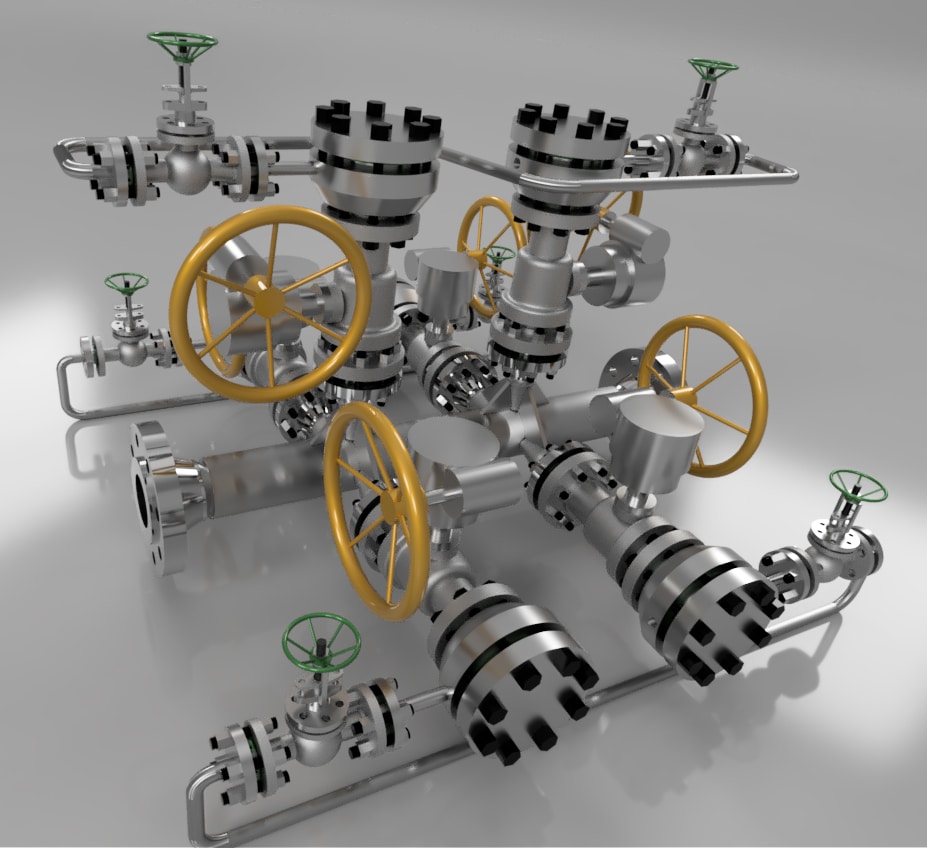
Based on our proven track record at the facility in many different units, and our ability to meet all of the customers requirements, ValvTechnologies has been selected as best suited for the application. Valves are expected to ship after completion of the new unit, by end of the year.