Including pressure relief valves at critical points within fluid systems can prevent blowouts, equipment damage, or system failures. That is why it is important to understand when relief valves should be activated and where they should be used to maximize chemical plant safety.
Why Relief Valves May Be Activated
There are many reasons why complex, large-scale fluid systems can overpressurize, most of which fall into one of the following categories:
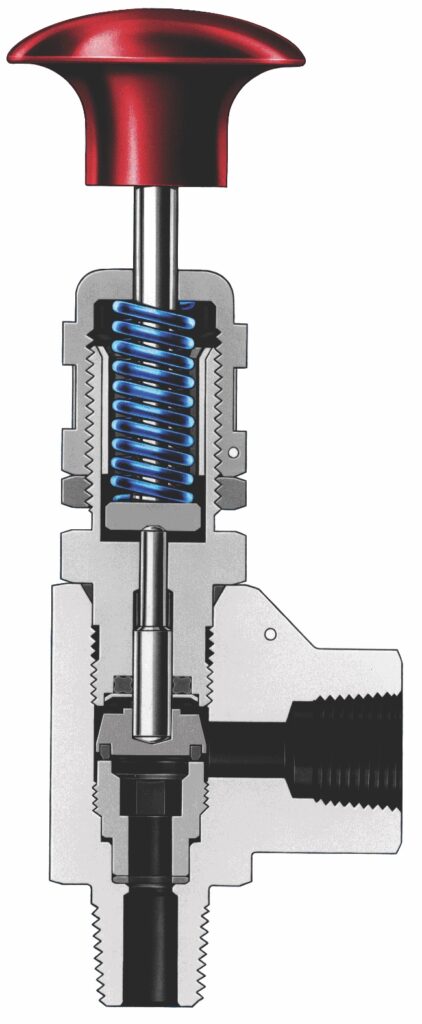
Procedural Error. Since people operate and maintain the systems, simple human error can be the reason why a system overpressurizes. Though robust fluid system training can help reduce the number of mistakes that occur, accidents still happen. When they do, it is imperative to have relief valves installed to prevent that error from creating an unsafe condition in the system.
Component Wear. Over time, fluid system components will naturally wear, especially in systems that handle aggressive chemicals. Worn components can compromise pressure control, and relief valves can help manage the potential pressure changes that may result.
Contamination. Regulators can sometimes become compromised by dirt or other contaminants, which may affect their performance. Their seals can be affected, which can lead to unwanted pressure making it past the seat. When that happens, the downstream pressure could rise. A relief valve would release the unwanted pressure and prevent an unsafe buildup of pressure.
Loss of Power. If the fluid system depends on electrical control of some components for pressure control, an unexpected loss in power can cause pressures to rise sharply. Having safety controls like relief valves can prevent a loss of power from crippling the plant.
Where Relief Valves Should Be Installed
Proper placement of relief valves is crucial to ensuring the safety of fluid systems, but which applications truly require them? Relief valves should be installed within the following applications:
High-Pressure Systems. When fluid system applications exceed specified pressure levels, relief valves are an essential safety element to stop potential accidents. In the case of high-pressure systems, relief valves can supplement high-quality, small-bore tube fittings to prevent pressures from rising beyond preset levels.
Toxic Fluids or Chemical Applications. For fluid systems that handle toxic or hazardous chemicals, relief valves are essential to preventing the accidental release of these fluids into the atmosphere. They can be used to protect operators and technicians, and the released fluid can be captured and disposed of safely.
Sensitive Equipment. Analytical equipment is some of the most sensitive in a plant, and it is crucial to protect it from overpressurization. This equipment is often installed after a significant investment by the plant, and inadvertent damage caused by too much pressure can be costly. Properly rated and set relief valves can help reduce fluid pressures before they reach the analytical equipment, eliminating the potential for damage.
How to Optimize System Design for Chemical Plant Safety
Incorporating pressure relief valves at the appropriate places within your industrial fluid system is a good way to improve chemical plant safety and should be accounted for during initial system design. To decide how and where relief valves should be installed in your plant, you should work with a qualified supplier who can advise you on the best way to design your system. Planning ahead, under the guidance of a fluid system expert, will save you time and money in the long run.