Enabling safe, reliable operation of these hydrogen systems means using high-quality ball, needle, and check valves – in conjunction with other hydrogen-qualified components with material integrity and compatibility – that will deliver leak-tight performance for years or even decades:
Hydrogen Ball Valves: Used to start and stop flow, ball valves are common in hydrogen systems. Look for stem seal designs that are highly resistant to wear to enable long-term performance. This includes trunnion-style ball valves with a direct-load design that enables reliable leak-tight performance. Valves with a bottom-loaded stem design can also enhance safety by limiting potential stem blowouts. Ask your supplier to help guide your selection, as you may need 2- or -3-way functionality, different mounting options, and a specific flow coefficient range to meet your needs.
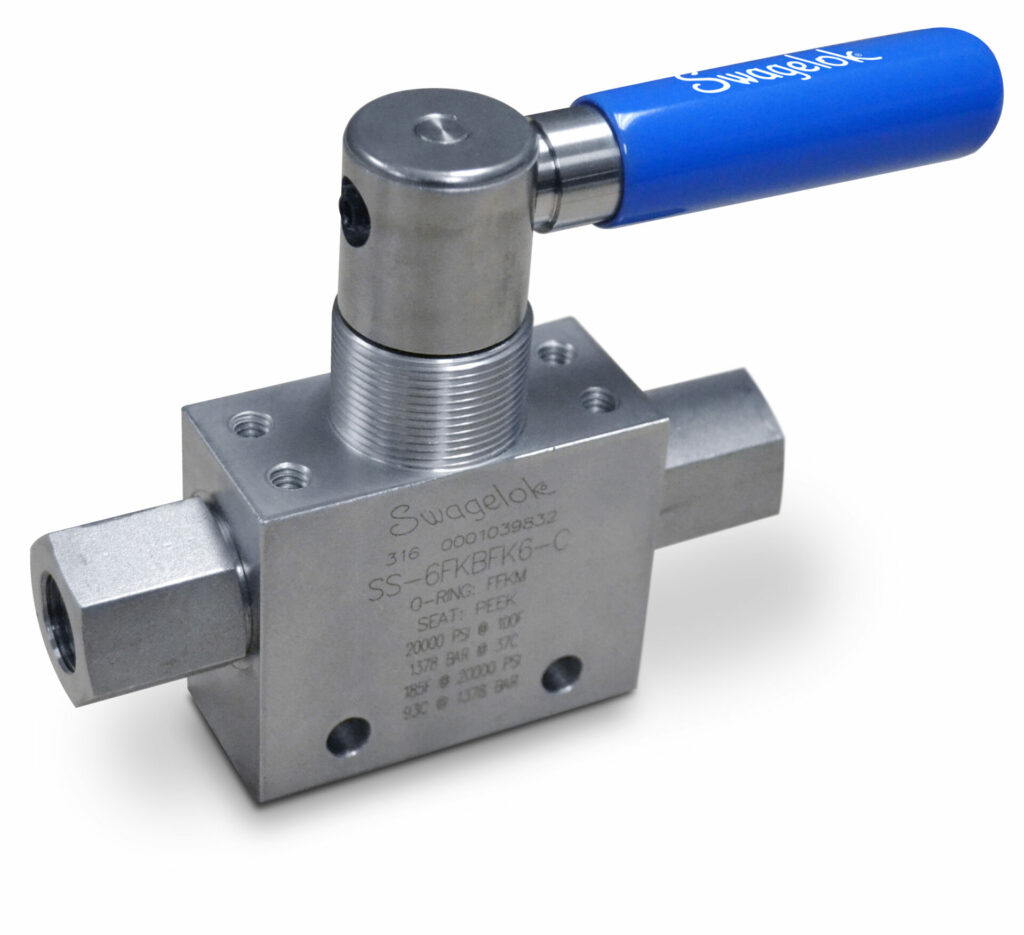
Hydrogen Needle Valves: For fine fluid flow adjustments, needle valves enable precise control. They are typically all-metal in construction and require a large amount of force to seal properly. This force could potentially deform the needle and even the seat, causing the valve to not achieve a positive shutoff. With that in mind, operators should look for needle valves made from high-quality 316 stainless steel that can resist deformation during repeated use. It’s also important to choose valves that are qualified for elevated working pressures, as common hydrogen applications operate in the 350 bar to 700 bar range.
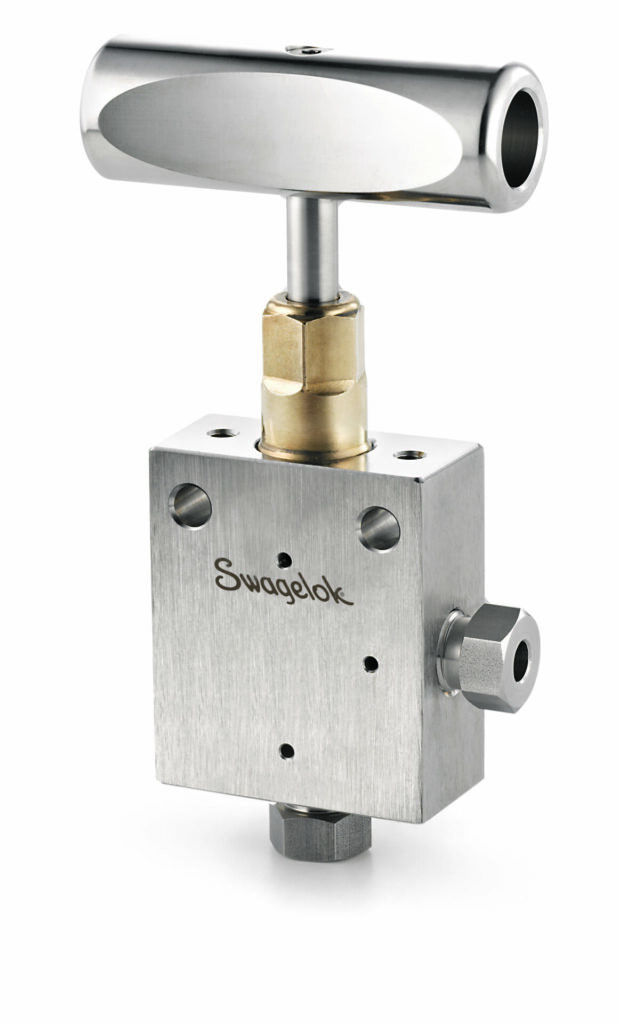
Hydrogen Check Valves: Commonly used in hydrogen compressors in refueling systems, check valves perform the essential safety function of controlling excess backflow to protect personnel and assets. This functionality requires large, fast temperature and pressure changes, creating elevated stress on the valve’s elastomer seals. Additional stress may occur on the springs used in most check valves, as they are often made from strain-hardened metals that are more susceptible to hydrogen embrittlement than high-quality 316 stainless steel. For these reasons, ball check valves are more suitable forhydrogen compressors, ensuring all materials are compatible for the application.
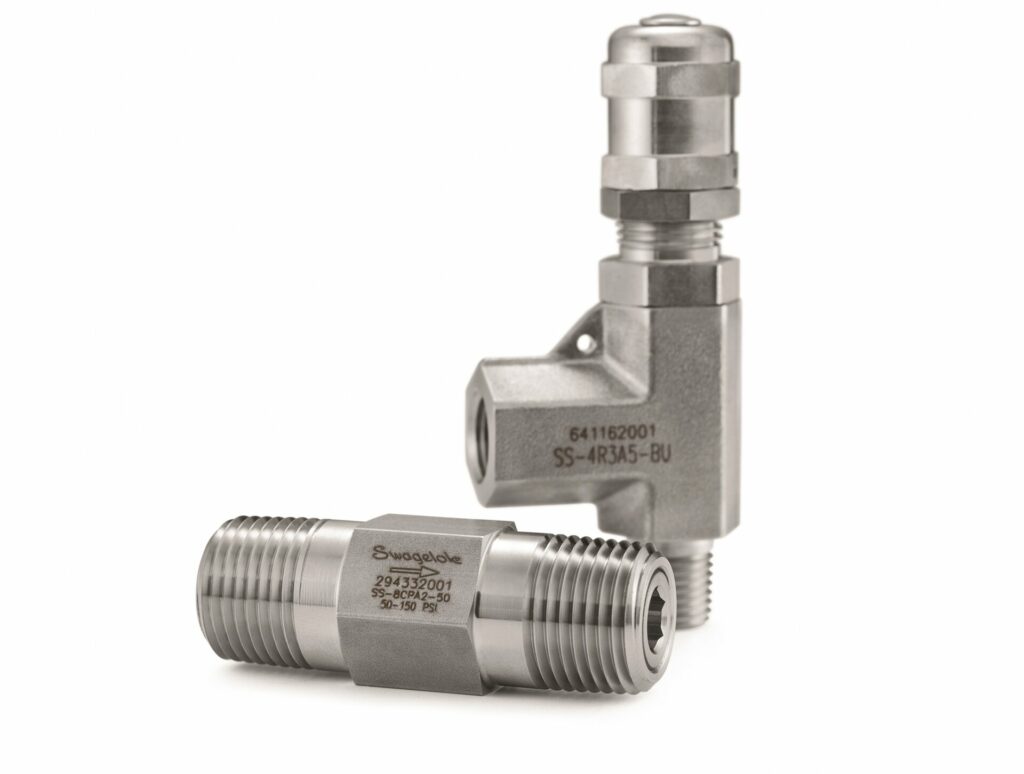
Selecting and specifying the right components for all hydrogen systems will deliver the safety, reliability, and durability the hydrogen mobility fuel market requires to enable its long-term viability. When making selections for your hydrogen systems, be sure to work with a supplier that can offer a range of ball, needle, and check valves that are suitable for your specific hydrogen service needs. This includes offering a complete portfolio of additional components that will also help to make your hydrogen systems safer and more reliable.