In many countries, in addition to a global health crisis, the COVID-19 pandemic has caused a shortage of toilet paper and a huge increase in clogging problems. Indeed wastewater treatment plants are getting clogged with toilet paper alternatives that people are using, such as wipes, tissues, napkins, and paper towels. Everywhere in the world, we have read, for the past few months, on social networks and press that “even though the package may state ‘flushable,’ these items do not break down like toilet paper and create plumbing problems!”
These pump clogging issues that are being experienced in many countries today were addressed and resolved years ago by a French innovator, Stephane Dumonceaux, GM of SIDE Industrie and inventor of the DIP Systeme®. The first DIP Systeme® was patented, installed, and proven successful in 2003 and since then there are over 2,000 of these systems in use in municipalities (for example in Disneyland Paris) throughout France as well as in the USA, Canada, Cambodia, Portugal, Ivory Coast, Caribbean Islands…Based on practical expertise in the field, the development of its product range (56 models with flow rate: from 2 to 2000 m3/h (20 to 10.000 GPM)/unit and head from 1 to 110m (3 to 300 ft)) is the result of 35 years of research, and from listening to the daily concerns of its 2,000 users worldwide, enabling them today to offer a modern alternative to wastewater lift stations that saves time and money by logically solving issues such as dangerous gases (H2S), odors, sand and grease accumulation, hazardous access, variable flow, clogging, and dirty jobs…
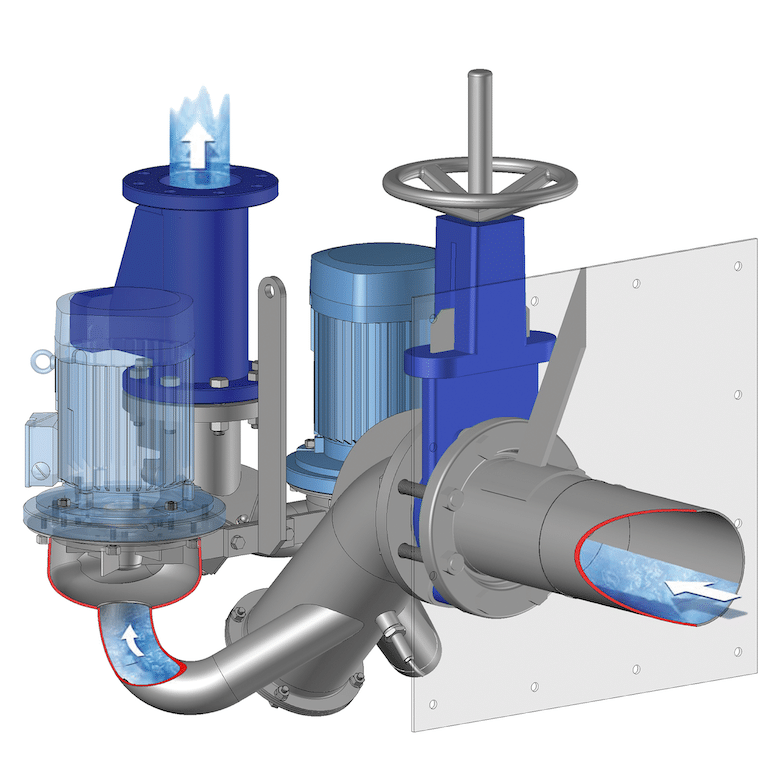
How? Because DIP Systeme® lifts and boosts variable flows from the sewer line invert to the discharge pipe with no need of any wet well. By lifting gravity effluent directly at the point of entry, without water loading or a wet well, the DIP Systeme® overcomes the drawbacks of retained volumes of effluent such as dangerous gases (H2S), smells, sand and grease accumulation, equipment corrosion, structural erosion, clogged floaters; and offers access safety. The absence of a collection tank eliminates costly cleaning operations of traditional units and eliminates in the same time the complaints from residents living close to an installation that produces unpleasant odors and the risks for maintenance technicians. Indeed, in comparison to the DIP System, traditional lift stations use submersible pumps in a wet well: the pumps are activated by float switches when the water reaches a preset level. The pumps then run at full speed to empty the wet well. A primary issue with submersible pumps in wet wells is clogging with wipes and other flushable materials.
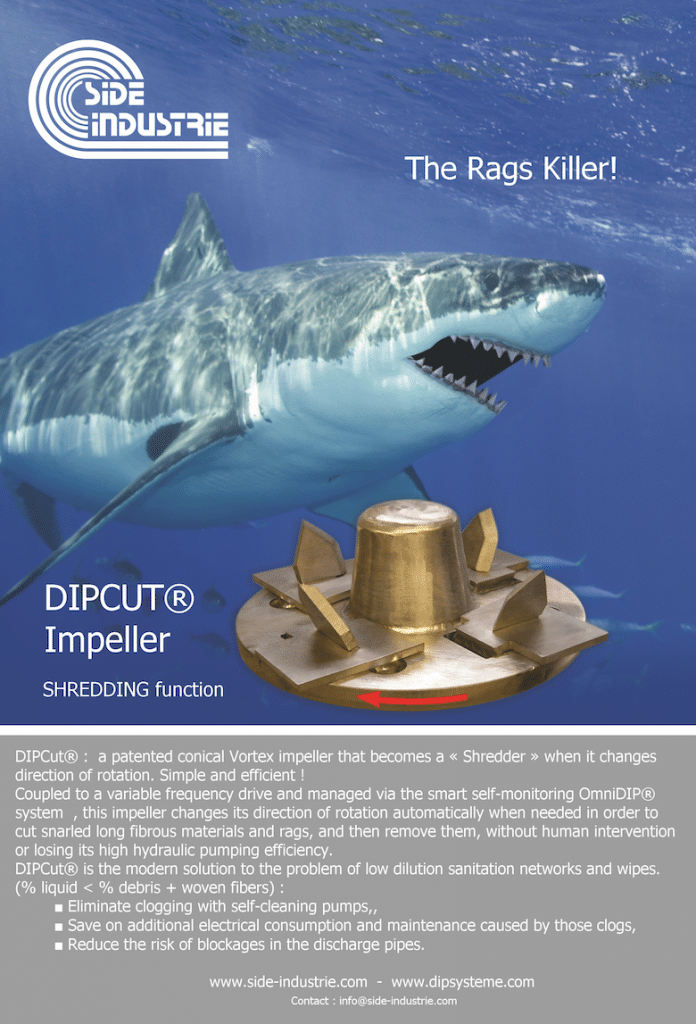
On top of the absence of a wet well, with the DIP System, there are much less clogging problems, as in 2012 SIDE Industrie designed the DIPCut®: a patented impeller that becomes a “Shredder” when it changes the direction of rotation. Coupled to variable frequency drive, this impeller changes its direction of rotation automatically when needed in order to cut snarled long fibrous materials and wipes, and then remove them. This is the ideal “Rags-Killer”! DIPCut® combines the advantages of the conical Vortex impeller when pumping sand, gases, or big solid wastes and the shredding function cutting long fibrous materials into shreds. DIPCut® allows the savings of those clogs and uses less power!